
How Is a Hydraulic Press Machine Made?
Before we get into a discussion of how a hydraulic press machine is made, we will first discuss what exactly a hydraulic press machine is and what is it used for.how to make a hydraulic press machine.
A hydraulic press is defined as:
Simply put, it’s a hydraulically powered mechanical machine used for metal packaging. The most basic definition of a hydraulic press is a machine with a flat surface that can be used to pack, fasten, or crush metal. The majority of factories today employ hydraulic presses because of their many benefits.
Many different kinds of work require the use of a hydraulic press. Hydraulic presses can be used for a variety of purposes, from building to compacting. Only a handful of settings and professions utilizing a hydraulic press will be discussed here.
Fabricating Metal for Automobiles
Fabricating metal components for automobiles is one application for hydraulic presses. A hydraulic press can be used to manufacture everything from windshield wiper blades to grab handles.
Many products are formed and assembled using hydraulic presses. Not just auto components, but a wide variety of electrical components are included. A hydraulic press may even be used to manufacture your thermostat.
Use of Liquids in Hydraulics
Liquids are excellent candidates for use in a hydraulic press due to the fact that they are not easily compressed. The operation of the hydraulic press is caused by applying a little amount of force to the Plunger, which in turn forces the fluid that is located underneath.
In the end, the lifting of the Ram is accomplished through the application of force in a uniform manner. The object is positioned so that it is in the path of both the Plunger and the Ram, both of which exert a crushing force on the thing.
Hydraulic Pressing in Mechanical Use
A wide selection of hydraulic presses is available to meet mechanical needs. Some examples of hydraulic presses are arbor presses, overlaying presses, C-outline presses, pneumatic presses, and H-frame presses.
When using a hydraulic power press, the entire ram may be pressed smoothly and uniformly. Many hydraulic presses have pressure-limiting strain relief valves installed to prevent damage to the framework from excessive force.
Multiple hydraulic presses make use of a double-acting chamber to raise a tooling-joined ram. Simply by considering the desired output, desired output speed, and desired output strain, a suitable hydraulic press can be selected.
Appliances that use hydraulic presses include refrigerator panel molders, microwave oven molders, dishwasher molders, and clothing machine molders.

Electrical Component Assembly:
Hydraulic presses are used to collect housings and switches for use in switching stations. The same cycle is used in the production of thermostats.
Producing Ceramics:
Hydraulic presses that operate at room temperature can replace the traditional method of producing ceramics, which involves the use of heat furnaces that operate at temperatures higher than 1800 F.
Hydraulic presses will pack earthenware products such as concrete tiles for bathrooms, blocks, and other similar materials. It packs it into the ceramic framework using this technology, which requires minimal strain and less labor.
Hydraulic presses are used for auto-collapsing and framing applications, such as assembly. Hydraulic presses are used to produce a variety of automotive components, such as:
- Fasteners
- Vibration dampeners
- Brake pads
- Embed forming
- Floor mats and coverings
- Truck bed liners
- Electrical connectors and covers
- Gasoline conveyance parts, and many more.
A Detailed Understanding of the Components of a Hydraulic Press:
A hydraulic press is a name given to a piece of machinery that applies compressive force through the use of a hydraulic cylinder. The press table, the hydraulic cylinder, and the frame are the three components of a hydraulic press that are absolutely necessary.
For the purpose of this project, the press frame, cylinder, and press table are all created through the design process. Their productivity and level of quality in the work they do with the press are being examined so that they can be improved.
You will be able to reduce the cost of your hydraulic press by reducing the amount of material that is used in its construction. You may accomplish this by making more informed design decisions while you are drafting the press’s components.
Efforts have been made in this regard with the goal of lightening the load. In this investigation, the primary focus is on a project to reduce the overall mass of an H-frame hydraulic press, which has applicability in the real-world industrial setting. The forces that are acting on the working plates need to be counteracted by this press, and it also needs to comply with very specific guidelines.
Implementation is used in the application for the purpose of doing analysis and optimization on a hydraulic press. The purpose of the research is to find a way to merge the mechanical system of a hydraulic press with its hydraulic system.
This will make the press simpler to operate and allow for the production of a greater number of smaller parts in larger quantities. In today’s world, achieving a deadline is one of the most important factors that determine the success of a manufacturing operation.
Automation, which frees up workers’ attention to focus on other duties, enables production times to be reduced without a corresponding decrease in quality or even an increase in the latter. As a result, with the assistance of the hydraulic system, an effort has been made to ensure that the press job operates in a manner that is both smooth and quick.how to make a hydraulic press machine.
The Construction of a Hydraulic Press and Each of Its Components Individually
It is recommended that prior to learning how to use a hydraulic press, one should become familiar with the different elements and components that make up the press. A hydraulic press may be broken down into its component elements, and the following is a summary of those parts and how they work together to produce the press:
1. The Switch for the Upper Limit Bound
With the assistance of the limit switch, the height and width of the material that is being pressed between two plates can be adjusted to produce a different thickness of the material. In addition to this, the force that is applied to the workpiece is controlled by maintaining a consistent space between the press plates.
2. Oil storage:
The oil tank supplies the oil that goes into the oil cylinder. It’s a tube that extends all the way from the cylinder’s piston rod to the outside of the machine. The rod is what applies force to the press plates, and the tube connects the tank to the rod so that oil can be transferred there.
3. Motor:
The pressure that is essential to the production of mechanical power is generated by an oil pump, which is powered by a motor.
From the top, moving clockwise, the pressure gauge is used to get a reading of the pressure in the hydraulic press’s tank. Releasing the safety catch releases any strain that may have been placed on the material that is being pressed or on any component of the hydraulic press.
4. Control panel for electric devices:
The electrical control box is where all of the signals that are transmitted to modify the settings on the system are sent. The settings can be adjusted in a number of different ways. It is made up of a system of wires and circuits that connect the several levers and switches that are there.
5. Component mechanized with a valve controlled by the user:
With the assistance of a manual control valve, one is able to make adjustments to the pressure that is being applied to the workpieces. This is accomplished by controlling the amount of pressure that is applied to the press plates by regulating the flow of oil, which can either be restricted or redirected.
6. Survival space:
The process that the material goes through that causes it to change in size and shape is precipitated by the application of pressure from the hydraulic cylinder as it is being pushed through the bailing chamber.
7. Plate made of steel for use in pressing:
The pressing plate applies pressure to the material that is being pressed, which allows for the material’s size to be either decreased or enlarged according to the desired effect. Because of the little amount of surface area that is in touch with the object, only a light amount of pressure should be given at a time. You are free to attempt something multiple times until you achieve the results you are looking for.
8. Safety Catch:
The primary objective of the safety door is to ensure people’s safety by facilitating easy access to the area behind the door in order to perform maintenance or repairs.
In a hydraulic cylinder, when it is necessary to provide force in the form of a cylindrical motion to bring components closer together, a hydraulic cylinder is the device that fulfills this function.
Metal is the primary material used in its construction, and it has both a piston rod and an outside metal casing. The primary function of the cylinder is to apply pressure to the material by converting the force exerted by the hydraulic fluid into mechanical energy.
Now that you are aware of how to make a hydraulic press machine, you can go ahead and learn more about its uses and consider getting one for yourself at GUANGDUAN.
CONTACT US

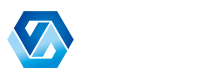
Guangdong Metal Forming Machine Works Co., Ltd.
We are always providing our customers with reliable products and considerate services.
If you would like to keep touch with us directly, please go to contact us