
Straight Side Double Point Multi-Station Precision Engineering Press Machines Sets New Industry Standard
What exactly is the Straight Side Double Point Multi-Station Press?
The GD2 press is a modern machine designed for precise manufacturing tasks. Its main parts include the machine body and slide, made from high-quality steel plates welded together. Because of this, the press is strong and durable. For machines with capacities over 600 tons, the body comes in separate parts connected by pull levers. This design makes the press easy to move and install. But why is this important for modern manufacturing? Could this type of structure significantly improve production quality and efficiency?
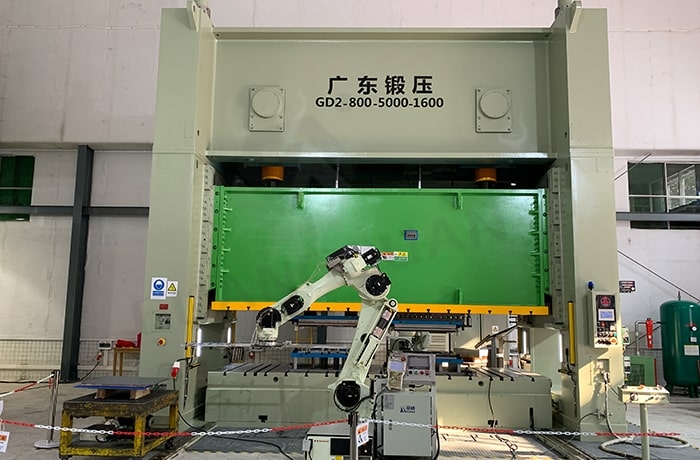
Innovative Design and Cutting-Edge Technology
Key Features of This Press
The press uses two-level gear transmission. Because of this, the slide can move faster and more times in each cycle. It has a wider space between the crank and connecting rod. This design helps the machine handle unbalanced loads easily. Also, it helps keep the precision of the machine stable for a long time.
The slide uses an eight-surface guiding system. With this, side forces are lower, and precision stays high. It can also include a multi-section air cushion. This air cushion helps especially in multi-station stamping work. Besides that, the machine can have an upper knockout cylinder fitted to the slide block.
This press is mainly used for sheet metal stamping. It works especially well in automated processes. Examples include progressive die stamping and multi-station stamping. It also has special interfaces ready for two-dimensional and three-dimensional servo production lines. So, it can easily connect to modern automation equipment.
Advanced Engineering for Better Performance
The press uses an eight-surface full-guideway guiding system. This system makes the slide stronger against uneven loads. It also lowers side forces, making the machine more accurate. With this feature, the precision of the press can last much longer.
Unmatched Accuracy and Efficiency
How the Machine Keeps Precision in High-Volume Work
The press uses two-level gear transmission. Between these gears, an extra set of idler gears is added. This design widens the space between pressure points. Because of this wider space, the press can handle uneven loads better. This is very helpful for multi-station and progressive die stampings.
Besides that, this design helps lower the total height of the press. It makes the machine more compact overall. Since it is compact, it also saves space on the production floor. Do you see how this compact design can be helpful in factories?
Benefits for Manufacturers Looking for Reliability
Manufacturers who use this press can get consistent results. It gives high precision even after many cycles. Because of the simple and strong design, the machine doesn’t lose accuracy over time. For companies, this means fewer mistakes and better quality.
Also, the machine can handle heavy workloads easily. Even when the stamping is unbalanced, precision remains high. Manufacturers can trust this machine to keep their production stable.
Robust Construction for Long-Term Performance
Durable Materials and Strong Build Quality
This press uses strong materials for long-lasting use. The frame and main parts are built from high-quality steel plates. They are welded together carefully to make the structure strong. This gives the machine good strength and stability. Because of this, the machine can run for many years without problems. It can also handle heavy loads without bending or breaking. The materials used make sure the machine stays precise and reliable. Manufacturers can trust this press for long-term performance in factories.
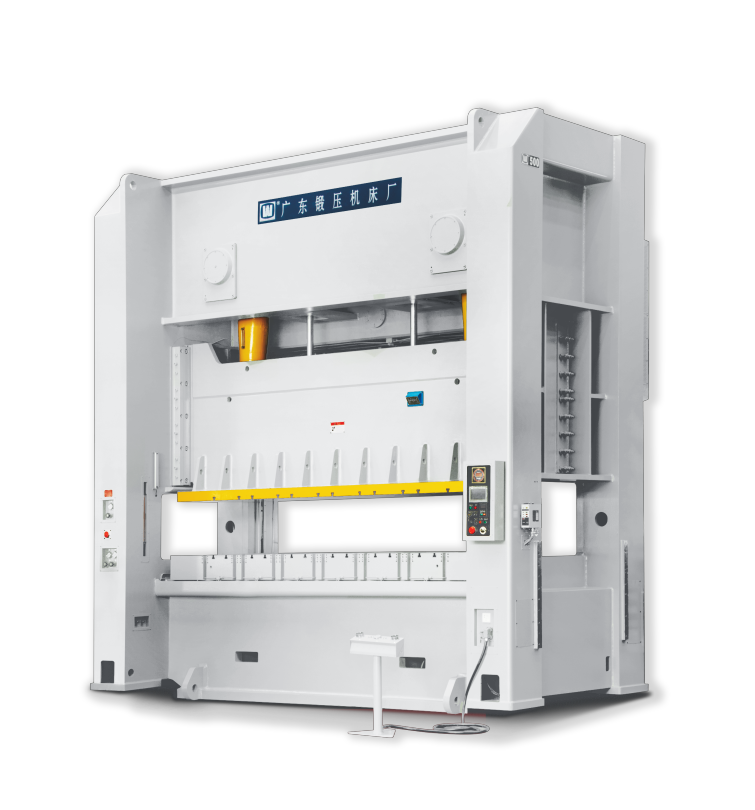
Special Die Cushions for Multi-Station Presses
The upper and lower die cushions in this press are designed for multi-station operations. Each die cushion gives strong force, but the size of the cushion is small. This helps the machine handle different step distances easily. Also, each die cushion has a long service life and stays accurate for a long time. It reacts quickly when working, which keeps production fast. Pressure fluctuations are small. Because of that, operations are smooth and consistent. Operators can adjust the pressure of each cushion separately. This feature gives flexibility in production. Companies can use this to handle different types of metal stamping tasks easily.
Longer Lifespan and Lower Maintenance Costs
The strong design and high-quality materials help extend the lifespan of this press. Its parts do not wear out easily. Because of this, the machine can run continuously without frequent maintenance. This reduces costs for companies. The structure helps the press stay precise over long periods. This means fewer mistakes in production. Manufacturers save money by avoiding downtime and repairs. Also, the simple design makes maintenance easier when it is needed. Workers can quickly fix or replace parts, saving time and effort.
Versatility Across Industries
Use in Automotive, Aerospace, Electronics, and Other Industries
This multi-station press is very versatile. Many industries can use it effectively. The automotive industry often uses it for stamping car body parts. Aerospace companies use it for precision metal forming. The electronics industry uses this press for creating precise metal parts needed in electronics devices. Additionally, industries like home appliances and metal furniture also benefit from this press. The press is strong enough for large metal parts but accurate enough for smaller, detailed components. Companies from different fields can rely on its accuracy and strength for their specific needs.
Suitable for Different Metal Forming Processes
The design of this press makes it suitable for various metal forming tasks. It can easily handle progressive stamping, where metal sheets move from one station to another. It also works well in blanking and drawing operations. Each process requires different types of pressure and precision, but this press can handle all these needs. Companies do not need separate machines for different tasks. Instead, they can use one versatile machine. This flexibility helps manufacturers save space and money. Operators can quickly adjust the settings to change between processes. This adaptability makes the press valuable for factories doing multiple kinds of metal forming.
Sustainability and Energy Efficiency
Environmentally Friendly Innovations in Press Technology
This press includes several eco-friendly features. One important feature is the wet-type clutch. The clutch uses friction plates filled with oil. This design gives the clutch a strong turning power. It also helps the clutch last longer because there is less wear.
The clutch uses many plates, but it still reacts quickly. It starts and stops easily. The connection is also very stable. Workers can start and stop the machine many times without causing problems. Because of this, it is perfect for continuous factory operations.
This clutch also protects the environment. It produces very little pollution. It operates quietly, which is good for workers. It meets environmental rules and standards, making it better for factories and the planet.
Reducing Energy Use and Waste
This machine also saves energy. Its special clutch design helps it run smoothly without using too much power. It reduces energy consumption because it is efficient. It does not waste energy during operation. Less energy use also lowers production costs.
In addition, the press does not produce much waste. Its parts last longer, so fewer replacements are needed. Companies can save money because fewer parts need changing. Less waste also helps factories stay cleaner. This is better for the environment and the company.
Enhancing Global Manufacturing Standards
Setting New Standards in Manufacturing
This press is helping improve manufacturing standards around the world. It combines high precision with strong performance. Because of its accurate and reliable features, it sets a new standard for other machines to follow. Manufacturers who use this press can achieve high-quality production easily.
The press is strong and precise, helping companies meet strict industry requirements. It gives factories reliable equipment that improves product quality. This reliability helps businesses compete better globally.
Global Use by Leading Manufacturers
Leading manufacturers around the world already use this press. It is popular because it offers accuracy and reliability. Companies in automotive, electronics, and aerospace industries prefer it. They trust this press to produce high-quality metal parts consistently.
This wide use by top global companies shows the machine’s reliability and efficiency. It has become a valuable part of many modern factories. Other companies see this success and choose this press to improve their production processes.
Upgrade Your Production Today!
Choose the GD2 Multi-Station Press. It is strong, precise, and saves energy. Many top manufacturers already use it. Improve quality, reduce costs, and protect the environment. Make your factory better now!
CONTACT US

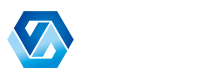
Guangdong Metal Forming Machine Works Co., Ltd.
We are always providing our customers with reliable products and considerate services.
If you would like to keep touch with us directly, please go to contact us