
What Impact Does High Pressure Press Have on Product Quality and Efficiency?
In the realm of manufacturing, the quest for precision and intricacy drives innovation. High pressure press technology stands at the forefront of this pursuit, offering unparalleled capabilities in shaping metals to exact specifications. This blog delves into the significance of high-pressure presses in industries like hardware and electric appliances, stainless steel ware, electronic components, and motor manufacturing. As we explore these sectors, we’ll uncover the challenges they face and how high-pressure presses address their needs.
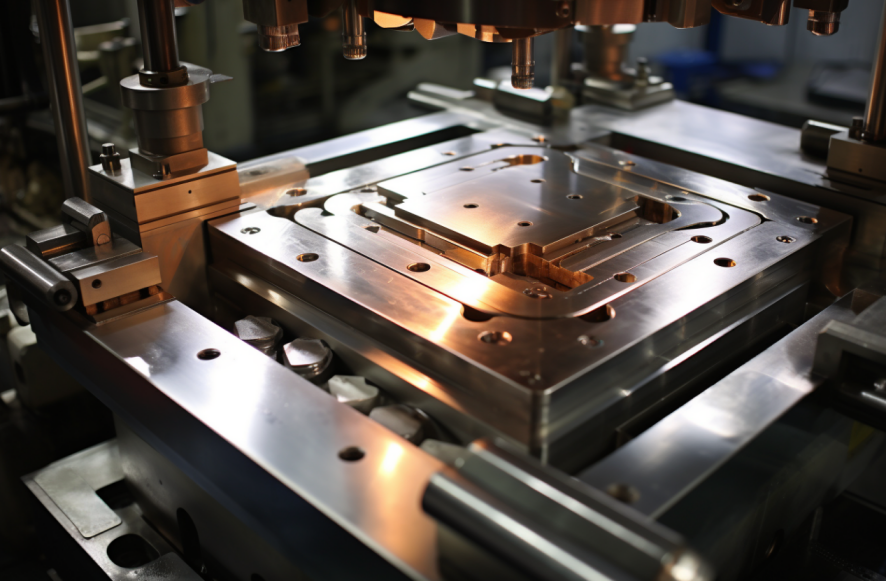
Market Needs Analysis
1.1 Rising Demand for Precision-Engineered Components
In the hardware and electric appliance industries, the demand for precision-engineered components is escalating. Consumers seek products that not only function flawlessly but also boast aesthetic appeal and durability. High-pressure presses enable manufacturers to meet these expectations by crafting intricate parts with utmost accuracy and consistency. From intricate casings to precisely engineered gears, these presses play a pivotal role in elevating the quality of hardware and appliances.
1.2 The Significance of High-Quality Stainless Steel Ware
In the culinary and hospitality sectors, the importance of high-quality stainless steel ware cannot be overstated. From professional kitchens to upscale restaurants, chefs rely on durable, hygienic cookware to execute their culinary masterpieces. High-pressure presses ensure that stainless steel utensils are not only visually appealing but also resistant to corrosion and wear. With precise molding capabilities, manufacturers can create seamless designs that enhance both functionality and aesthetics.
1.3 Miniaturization and Complexity in Electronic Components
The realm of electronic components demands continuous innovation to keep pace with the ever-shrinking dimensions of consumer electronics and the increasing complexity of industrial applications. High-pressure press technology plays a vital role in this landscape by enabling the production of miniature yet intricate parts with precision and efficiency. Whether it’s microchips for smartphones or circuitry for industrial sensors, these presses ensure that electronic components meet the stringent requirements of modern technology.
1.4 Precision in Motor Manufacturing
Motor manufacturing spans automotive, industrial, and consumer product sectors, each with its unique demands for precision and performance. High-pressure presses are indispensable in crafting motor components with exacting specifications, from rotor cores to housing assemblies. With the ability to exert immense force and control material flow with precision, these presses enable manufacturers to produce motors that meet the rigorous standards of efficiency, reliability, and longevity.
Deep Drawing Challenges
2.1 The Role of Deep Drawing in Shaping Metal Components
Deep drawing is a fundamental process in metal forming, particularly in industries where intricate shapes and complex geometries are required. By exerting significant pressure on metal blanks, high-pressure presses facilitate the transformation of flat sheets into three-dimensional components with remarkable accuracy. This process is essential in creating a wide range of products, from appliance casings to motor housings, with minimal material waste and maximum efficiency.
2.2 Challenges of Deep Drawing Thin Plates
Despite its versatility, deep drawing thin plates presents several challenges, especially in industries where precision is paramount. Thin plates, while conducive to intricate designs, are susceptible to deformation and wrinkling under high pressure. Manufacturers must navigate these challenges by employing advanced techniques and materials to ensure uniform material flow and prevent thinning during the deep drawing process. High-pressure presses, with their precise control over force and displacement, offer a solution to these challenges, enabling the production of flawless components with consistent thickness and integrity.
2.3 Precise Control over Material Flow and Thinning
Central to the success of deep drawing is precise control over material flow and thinning, ensuring that the final product meets dimensional tolerances and surface finish requirements. High-pressure presses equipped with sophisticated control systems and die designs enable manufacturers to exert precise force distribution and optimize material flow, minimizing defects and enhancing product quality. By leveraging these capabilities, industries can produce deep-drawn components that meet the highest standards of performance and aesthetics
Forming and Aligning
3.1 The Essence of Forming and Aligning Processes
Forming and aligning processes are the backbone of manufacturing industries, shaping raw materials into intricate components with precision and accuracy. Whether it’s crafting appliance casings or motor housings, these processes are indispensable in achieving desired geometries and functional properties. However, when it comes to stainless steel components with intricate geometries, the challenges multiply. The inherent properties of stainless steel, including its high strength and resilience, pose obstacles to traditional forming and aligning techniques. High-pressure presses emerge as a game-changer, offering the precision and force required to shape stainless steel components with intricate geometries to exact specifications.
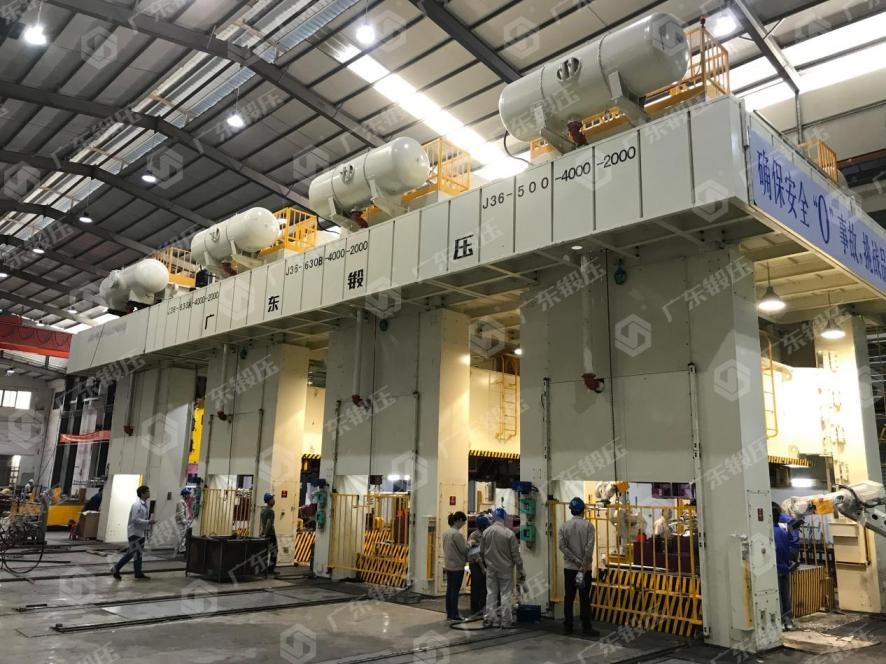
3.2 Challenges of Forming and Aligning Stainless Steel Components
Forming and aligning stainless steel components present a myriad of challenges for manufacturers. The high strength and hardness of stainless steel make it resistant to deformation, requiring substantial force to shape and align. Moreover, the intricate geometries of these components demand precise control over material flow and alignment to avoid defects and ensure dimensional accuracy. Traditional forming techniques often fall short in meeting these demands, leading to suboptimal results and increased production costs. High-pressure presses address these challenges by exerting immense force and providing precise control over material flow and alignment, enabling manufacturers to produce stainless steel components with unparalleled precision and quality.
3.3 The Role of High-Pressure Presses in Achieving Precise Forming and Alignment
High-pressure presses revolutionize the forming and aligning processes by offering the force and precision required to overcome the challenges posed by stainless steel components. Equipped with advanced control systems and die designs, these presses exert uniform force distribution and optimize material flow, ensuring consistent shaping and alignment of components. Whether it’s intricate appliance casings or complex motor components, high-pressure presses deliver the accuracy and repeatability needed to meet the stringent requirements of modern manufacturing. As industries continue to push the boundaries of innovation, high-pressure presses emerge as indispensable tools in achieving precision and efficiency in forming and aligning processes.
Bending Techniques
4.1 Understanding Bending as a Critical Manufacturing Process
Bending is a critical process in manufacturing various components, allowing manufacturers to shape materials into desired configurations with precision and efficiency. From automotive components to consumer electronics, bending plays a pivotal role in achieving the desired functionality and aesthetics of products. However, when it comes to bending stainless steel and thin electronic components, the challenges are abundant. The inherent properties of these materials, including their high strength and susceptibility to deformation, make traditional bending techniques ineffective. High-pressure presses emerge as a solution, offering precise bending capabilities while maintaining material integrity.
4.2 Challenges of Bending Stainless Steel and Thin Electronic Components
Bending stainless steel and thin electronic components pose unique challenges for manufacturers. The high strength and resilience of stainless steel make it resistant to traditional bending techniques, leading to deformation and defects in the final product. Similarly, thin electronic components, such as circuit boards and microelectronic devices, are prone to wrinkling and cracking during bending, compromising their functionality and reliability. Traditional presses lack the precision and control required to bend these materials without causing damage, resulting in increased scrap rates and production costs. High-pressure presses address these challenges by exerting precise force and providing advanced control over bending operations, ensuring that stainless steel and thin electronic components are bent to exact specifications with minimal distortion or damage.
4.3 How High-Pressure Presses Enable Precise Bending While Maintaining Material Integrity
High-pressure presses revolutionize the bending process by offering the force and precision needed to overcome the challenges associated with stainless steel and thin electronic components. Equipped with advanced control systems and tooling designs, these presses exert uniform force distribution and optimize material flow, ensuring precise bending with minimal distortion or damage. Whether it’s bending stainless steel sheets for automotive components or delicate circuit boards for electronic devices, high-pressure presses deliver the accuracy and repeatability required to meet the stringent requirements of modern manufacturing. As industries continue to innovate and evolve, high-pressure presses emerge as indispensable tools for achieving precision and efficiency in bending operations.
Conclusion
In conclusion, high-pressure press technology revolutionizes manufacturing across diverse industries by unlocking new possibilities in precision engineering. From hardware and appliances to electronic components and motors, these presses enable manufacturers to meet the evolving demands of the market with unparalleled efficiency and accuracy. As industries continue to push the boundaries of innovation, high-pressure presses will remain indispensable tools in shaping the future of manufacturing.
CONTACT US

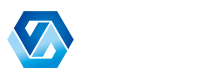
Guangdong Metal Forming Machine Works Co., Ltd.
We are always providing our customers with reliable products and considerate services.
If you would like to keep touch with us directly, please go to contact us