
What Is Shut Height In Press Tool
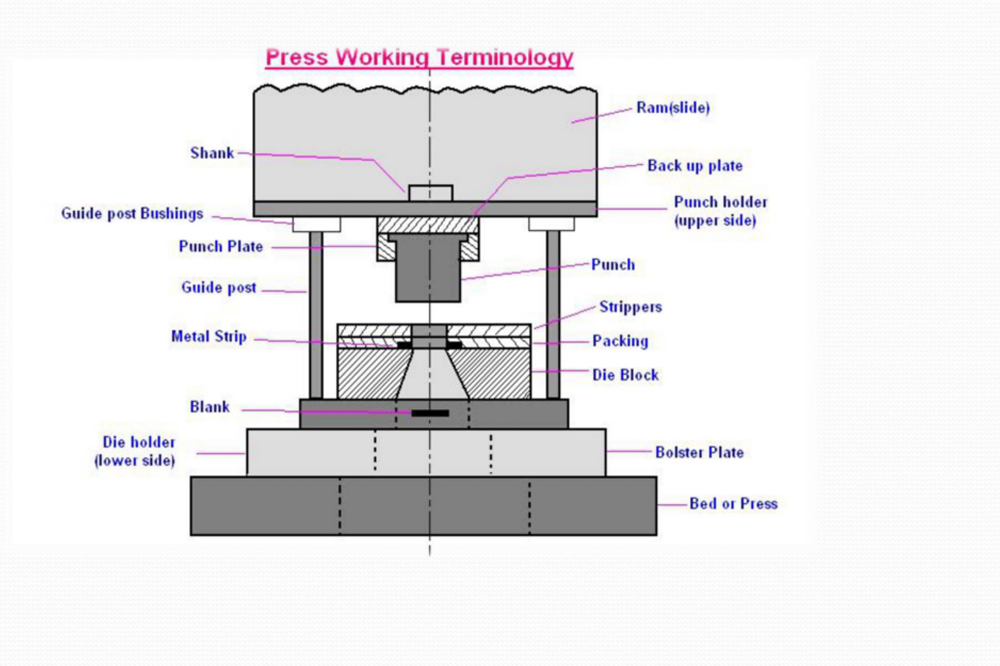
Shut height in press tool is a critical dimension that determines the quality of the pressed components. It is the distance between the top of the die and the top of the ram or bolster plate, and it plays a critical role in the press tooling process. Shut height is important because it influences the amount of material that can be worked, the die clearances, the speed at which the press can run, and the accuracy of the pressed part. It is important to understand shut height and its implications in order to optimize the press tooling process and ensure that the produced components meet the required quality standards.
What is shut height?
Shut height is the distance between the top of the die and the top of the ram or bolster plate. It is an important tooling dimension that determines the quality of the pressed components. It is a critical dimension that influences the amount of material that can be worked, the die clearances, the speed at which the press can run, and the accuracy of the pressed part. Shut height is important because it influences the amount of material that can be worked, the die clearances, the speed at which the press can run, and the accuracy of the pressed part. For example, in a full-cavity-depth die, shorter shut height allows for higher production rates and reduced die clearance. Shut height also affects the yield of the pressed components. If the shut height is too short, it can cause the dies to be overloaded and jam, causing deflection and misalignment of the dies. Similarly, if the shut height is too high, the dies won’t be able to move downward, which will result in incomplete press strokes. Thus, it is important to understand shut height and its implications in order to optimize the press tooling process and ensure that the produced components meet the required quality standards.
Importance of shut height
Shut height is an important tooling dimension that determines the quality of the pressed components. It is a critical dimension that influences the amount of material that can be worked, the die clearances, the speed at which the press can run, and the accuracy of the pressed part. Shut height is important because it influences the amount of material that can be worked, the die clearances, the speed at which the press can run, and the accuracy of the pressed part. For example, in a full-cavity-depth die, shorter shut height allows for higher production rates and reduced die clearances. Shut height also affects the yield of the pressed components. If the shut height is too short, it can cause the dies to be overloaded and jam, causing deflection and misalignment of the dies. Similarly, if the shut height is too high, the dies won’t be able to move downward and will thus result in incomplete press strokes. Thus, it is important to understand shut height and its implications in order to optimize the press tooling process and ensure that the produced components meet the required quality standards.
How to calculate shut height
Shut height is a critical dimension that determines the quality of the pressed components. It is important to understand shut height and its implications in order to optimize the press tooling process and ensure that the produced components meet the required quality standards. Shut height is a critical dimension that influences the amount of material that can be worked, the die clearances, the speed at which the press can run, and the accuracy of the pressed part. The shut height can be calculated by multiplying the die cavity depth of the die with the ram stroke. However, when calculating shut height, it is important to be aware of the difference between the die cavity depth and the ram stroke. The die cavity depth is the distance between the top of the lower die face and the bottom of the upper die face. The ram stroke is the distance between the top of the ram and the bottom of the bolster plate. These two dimensions need to be added together to calculate the shut height.
Factors affecting shut height
Shut height is an important tooling dimension that determines the quality of the pressed components. It is a critical dimension that influences the amount of material that can be worked, the die clearances, the speed at which the press can run, and the accuracy of the pressed part. Shut height is important because it influences the amount of material that can be worked, the die clearances, the speed at which the press can run, and the accuracy of the pressed part. For example, in a full-cavity-depth die, shorter shut height allows for higher production rates and reduced die clearances. Shut height also affects the yield of the pressed components. If the shut height is too short, it can cause the dies to be overloaded and jam, causing deflection and misalignment of the dies. Similarly, if the shut height is too high, the dies won’t be able to move downward and will thus result in incomplete press strokes. Thus, it is important to understand shut height and its implications in order to optimize the press tooling process and ensure that the produced components meet the required quality standards.
Minimum and maximum shut height
The minimum shut height should be the distance between the top of the lower die face and the top of the ram. The maximum shut height should be the distance between the top of the upper die face and the top of the ram. This difference is known as the die clearance. There are various factors that can affect the shut height. The materials used for the upper and lower dies and the thickness of the dies are some of the important factors. The material thickness of the die determines the amount of force required to press the material. Die material thickness also determines the minimum shut height. The required thickness of the upper and lower dies and the type of material used to make the dies can affect the shut height. Another important factor that can affect the shut height is the location of the bolster plate. The bolster plate is located between the upper and lower dies and provides support to the ram. The bolster plate location is critical to the shut height of the upper die. The top of the upper die should be 2-3 mm below the top of the ram.
How to adjust shut height
Shut height is a critical dimension that determines the quality of the pressed components. It is important to understand shut height and its implications in order to optimize the press tooling process and ensure that the produced components meet the required quality standards. Shut height is a critical dimension that influences the amount of material that can be worked, the die clearances, the speed at which the press can run, and the accuracy of the pressed part. Adjusting the shut height of the press can be done in different ways. The bolster plate of the press can be raised or lowered by a specified amount. The press ram can be retracted to a specific length. The die can be replaced with a die of a different height. Using these methods, the shut height of the upper die can be adjusted. However, remember that the lower die shut height must be adjusted as well because it influences the upper die shut height.
Quality control considerations for shut height
Shut height is an important tooling dimension that determines the quality of the pressed components. It is a critical dimension that influences the amount of material that can be worked, the die clearances, the speed at which the press can run, and the accuracy of the pressed part. Shut height is important because it influences the amount of material that can be worked, the die clearances, the speed at which the press can run, and the accuracy of the pressed part. For example, in a full-cavity-depth die, shorter shut height allows for higher production rates and reduced die clearances. Shut height also affects the yield of the pressed components. If the shut height is too short, it can cause the dies to be overloaded and jam, causing deflection and misalignment of the dies. Similarly, if the shut height is too high, the dies won’t be able to move downward and will thus result in incomplete press strokes. Thus, it is important to understand shut height and its implications in order to optimize the press tooling process and ensure that the produced components meet the required quality standards.
Effects of incorrect shut height
Shut height is an important tooling dimension that determines the quality of the pressed components. It is a critical dimension that influences the amount of material that can be worked, the die clearances, the speed at which the press can run, and the accuracy of the pressed part. Shut height is important because it influences the amount of material that can be worked, the die clearances, the speed at which the press can run, and the accuracy of the pressed part. For example, in a full-cavity-depth die, shorter shut height allows for higher production
CONTACT US

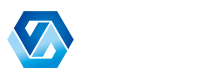
Guangdong Metal Forming Machine Works Co., Ltd.
We are always providing our customers with reliable products and considerate services.
If you would like to keep touch with us directly, please go to contact us