
Unlock the Amazing Power of Hydraulic Press Compression Molding!
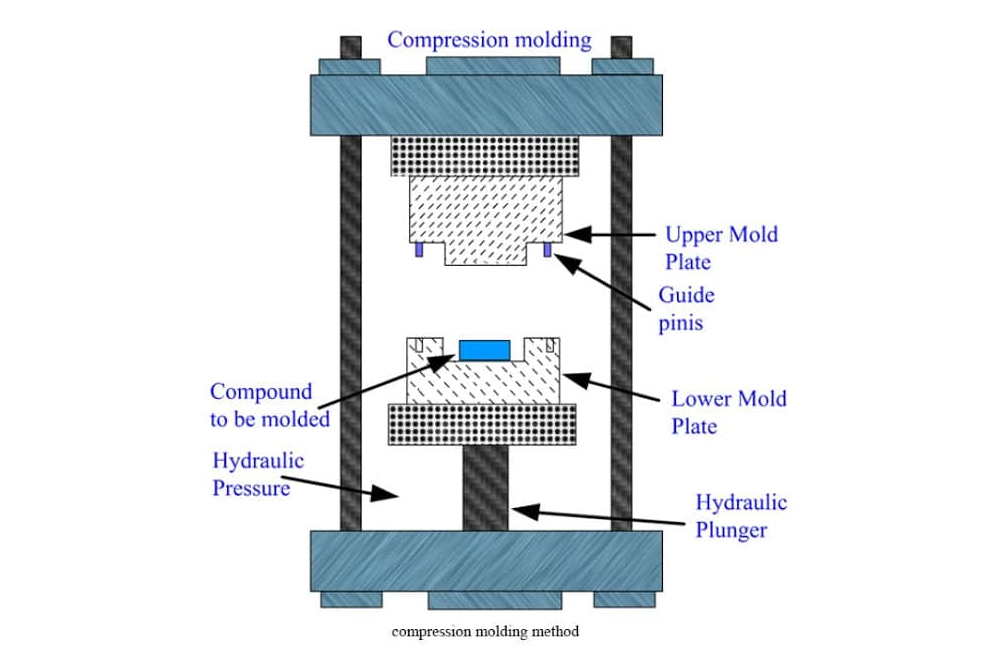
In today’s world of manufacturing, the demand for high-precision parts with strong physical properties is ever-increasing. From aerospace components to consumer goods, having the right materials and processes to create these parts is essential. One such process that is gaining popularity is hydraulic press compression molding. This article will explain what hydraulic press compression molding is and its many benefits, how it works, the types of molds that can be used, design considerations, materials used, processes involved, tips for improving results, and safety protocols.
Introduction to hydraulic press compression molding
Hydraulic press compression molding is a process used to create precision parts with strong physical properties. It involves pressing heated material between two molds using hydraulic pressure, resulting in a compressed, finished product. This process is widely used in the automotive, aerospace, medical, and consumer goods industries because of its precision and strength.
Hydraulic press compression molding has been around for decades, but it is becoming increasingly popular due to advances in technology, materials, and processes. With the right materials and processes, hydraulic press compression molding can be used to create complex shapes and parts with high accuracy and strength.
Benefits of hydraulic press compression molding
Hydraulic press compression molding has many advantages over other manufacturing processes. It is faster, more cost-effective, and more precise than other processes, resulting in parts with strong physical properties.
There are several advantages to using hydraulic press compression molding over other manufacturing methods. It is faster than other methods, resulting in faster turnaround times and lower costs. Because of its precision, it can produce complex shapes and parts with high accuracy and strength. It also requires less energy than other processes, resulting in lower energy costs. Additionally, it is more environmentally friendly than other processes, since it does not require the use of any hazardous chemicals or materials.
How hydraulic press compression molding works
Hydraulic press compression molding works by pressing heated material between two molds using hydraulic pressure. The molds are heated to a specific temperature and then the material is placed between them. The hydraulic pressure is then applied and the material is compressed into the desired shape.
The process is relatively simple but requires precise timing and temperature control. The molds must be heated to the correct temperature and the material must be heated to the correct temperature before it is placed between the molds. The pressure must also be applied at the right time and the right amount of pressure must be applied in order to achieve the desired results.
Types of hydraulic press compression molding
There are several different types of hydraulic press compression molding. The most common type is the two-part mold, which consists of two molds that are placed together and then heated and compressed. Other types of molds include the three-part mold, the four-part mold, and the five-part mold.
The two-part mold is the most common because it is the simplest and most cost-effective. The three-part and four-part molds are more complex and require more precise timing and temperature control, but they can produce more complex shapes and parts. The five-part mold is the most complex and requires the most precise timing and temperature control, but it can create the most complex shapes and parts.
Hydraulic press compression molding design considerations
When designing a part for hydraulic press compression molding, there are several design considerations that must be taken into account. These include the size of the part, the shape of the part, the material used, and the pressure required.
The size of the part must be taken into account when designing for hydraulic press compression molding. If the part is too large, it may not fit in the molds or the pressure may not be sufficient to compress the material. If the part is too small, it may not be able to withstand the pressure or it may not have enough surface area to be compressed properly.
The shape of the part must also be taken into account. If the part has complex shapes or sharp edges, the pressure may not be sufficient to compress the material or the part may not fit in the molds. Additionally, the material used must be able to withstand the pressure and temperature of the hydraulic press compression molding process.
Hydraulic press compression molding materials
The material used in hydraulic press compression molding must be able to withstand the pressure and temperature of the process. Common materials used in this process include metals, plastics, composites, and rubber.
Metals are the most common material used in hydraulic press compression molding because they are strong and durable. However, they are more expensive than other materials and may require more energy to heat and compress. Plastics are less expensive than metals, but they may not be able to withstand the pressure and temperature of the process. Composites are a combination of plastics and metals and may provide the best of both worlds. Rubber is a flexible material that can be used to create complex shapes and parts.
Hydraulic press compression molding process
The hydraulic press compression molding process consists of several steps. First, the molds must be heated to the correct temperature. Then, the material is heated to the correct temperature and placed between the molds. The pressure is then applied and the material is compressed into the desired shape. Once the shape is achieved, the molds are cooled and the part is removed.
The process must be carefully monitored to ensure that the correct temperature and pressure are applied. The temperature and pressure must be adjusted throughout the process to ensure that the part is compressed properly and that the desired shape is achieved. Additionally, the molds must be cooled in order to remove the finished part.
Tips for improving hydraulic press compression molding results
To get the best results from hydraulic press compression molding, there are several tips to keep in mind. First, the molds must be heated to the correct temperature and the material must be heated to the correct temperature before it is placed between them.
Second, the pressure must be applied at the right time and the right amount of pressure must be applied. Too much pressure can damage the molds and the part, while too little pressure will not result in the desired shape. Additionally, the molds must be cooled in order to remove the part.
Finally, the design of the part must be taken into account. If the part has complex shapes or sharp edges, the pressure may not be sufficient to compress the material or the part may not fit in the molds.
Hydraulic press compression molding safety
Safety is an important factor when it comes to hydraulic press compression molding. The molds must be heated to the correct temperature and the material must be heated to the correct temperature before it is placed between them. Additionally, the pressure must be applied at the right time and the right amount of pressure must be applied in order to achieve the desired results.
When working with hydraulic press compression molding, it is important to wear protective gear such as goggles, gloves, and long sleeves. It is also important to keep the area clean and free of debris to prevent accidents.
Conclusion
Hydraulic press compression molding is a powerful and precise process used to create precision parts with strong physical properties. It is faster than other methods, more cost-effective, and more precise, resulting in parts with strong physical properties. There are several types of molds that can be used, design considerations that must be taken into account, materials that can be used, processes involved, and tips for improving results. Additionally, safety protocols must be followed when working with hydraulic press compression molding.
If you are looking for a cost-effective and precise method of manufacturing parts with strong physical properties, then hydraulic press compression molding is a great option. With the right materials and processes, you can create complex shapes and parts with high accuracy and strength.
CONTACT US

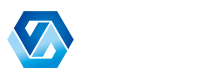
Guangdong Metal Forming Machine Works Co., Ltd.
We are always providing our customers with reliable products and considerate services.
If you would like to keep touch with us directly, please go to contact us