
The Growing Demand for Punch Machine: A Look at Global Trends
In an era where the pace of manufacturing operations accelerates rapidly, the importance of accuracy and operational efficiency cannot be overstated. Amid this technological revolution, one key driver of progress in metal shaping and stamping processes is the punch machine. The global demand for these machines is on an upward trajectory, fueled by a rising need for cost-effective and high-quality manufacturing solutions across multiple industrial sectors. Yet, the central question remains: what exactly is driving this growing necessity for punch machines, and how do advanced models like the Knuckle Joint Press Punch Machine GK Series factor into this expanding marketplace?
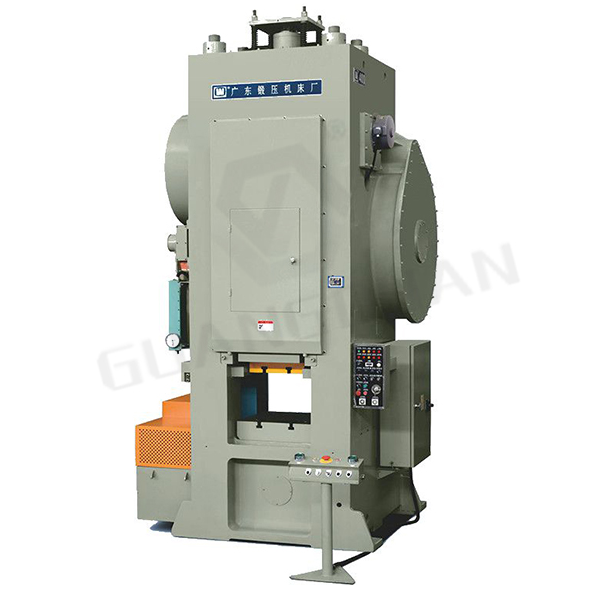
Global Market Demands and Shifting Trends
The worldwide manufacturing landscape is undergoing significant transformation, striving to keep up with the ever-increasing demands of industries such as automotive, aerospace, electronics, and consumer products. Companies in these fields are looking for machines that are not just durable and capable of producing large quantities, but also precise in execution. With technology advancing at an unprecedented rate, the quest for automation and the optimization of production lines has created a heightened demand for machinery that can deliver precise results repeatedly and reliably.
At the same time, as manufacturing trends move towards the use of lightweight materials and more intricate component geometries, there has been an increased emphasis on finding machines that offer both flexibility and efficiency. Especially relevant are machines designed to provide high precision, operate at quick cycle times, and work seamlessly across a range of materials. These machines are now the cornerstone of many advanced manufacturing processes.
Key Characteristics of Punch Machines
Punch machines, particularly the Knuckle Joint Press Punch Machine GK Series, have carved out a reputation for their ability to satisfy these contemporary industrial demands. These machines present an optimal blend of speed, precision, and robustness, essential for large-scale production environments. They play a pivotal role in forging and stamping operations, where the precision of every punch directly impacts the overall quality and consistency of the final product.
An In-Depth Look at the Knuckle Joint Press Punch Machine GK Series
The Knuckle Joint Press Punch Machine GK Series, distinguished by its sophisticated engineering and broad applicability, offers cutting-edge solutions to the modern manufacturing world. Developed by GUANGDUAN, this series comes equipped with a broad range of capacities and configurations that render it ideal for diverse applications, especially in fine stamping and extrusion operations.
Unique Attributes of the GK Series
One aspect that sets the GK Series apart is its wide range of forging press capacities, which span from 6300KN to 25000KN. This flexibility ensures that manufacturers can choose a model that fits their specific production needs, whether for smaller or larger components. Additionally, these machines offer bolster sizes ranging from 700mm by 700mm to 1200mm by 1200mm, further enhancing their adaptability to various production tasks.
Moreover, within the series, machines with a capacity from 4000KN to 16000KN utilize an integral structure, while the 12000KN model features a split structure design. This distinction allows manufacturers to select the best configuration based on their operational requirements, optimizing the machine for both performance and spatial considerations.
Distinctive Features of the Knuckle Joint Press Punch Machine
Pneumatic Wet and Dry Friction Clutch Brakes
One notable feature of the GK-630 series is the use of a pneumatic wet integrated friction clutch brake, whereas models ranging from GK-800 to GK-2500 incorporate a pneumatic dry split friction clutch brake. These mechanisms are crucial for ensuring that the machines maintain smooth and controlled operations, particularly during high-speed production cycles.
Crank Toggle Mechanism for Enhanced Precision
The machine’s mechanism employs a crank toggle system, which enables the slide to remain at the bottom dead center for about 1/18 of a cycle. This period of dwell is vital for achieving the maximum force and precision required in applications that demand fine stamping and metal forming.
Die Height Indicator and Ejector Device
Another standout feature is the die height indicator, boasting an accuracy display value of 0.01mm. Such precision is indispensable in fine stamping processes, where even slight inaccuracies can result in faulty parts. The inclusion of a mechanical lower ejector device as part of the standard configuration guarantees efficient and smooth ejection of parts post-stamping, thus optimizing productivity.
Why the Knuckle Joint Press Punch Machine GK Series Stands Out
The GK Series offers numerous benefits that make it a superior choice over conventional punch machines. Its precision, combined with its structural and control features, positions it as an exceptionally reliable machine for manufacturers aiming for consistent production of high-quality components. Furthermore, its ability to handle various materials and shapes underscores its versatility, making it suitable for a wide array of industrial applications.
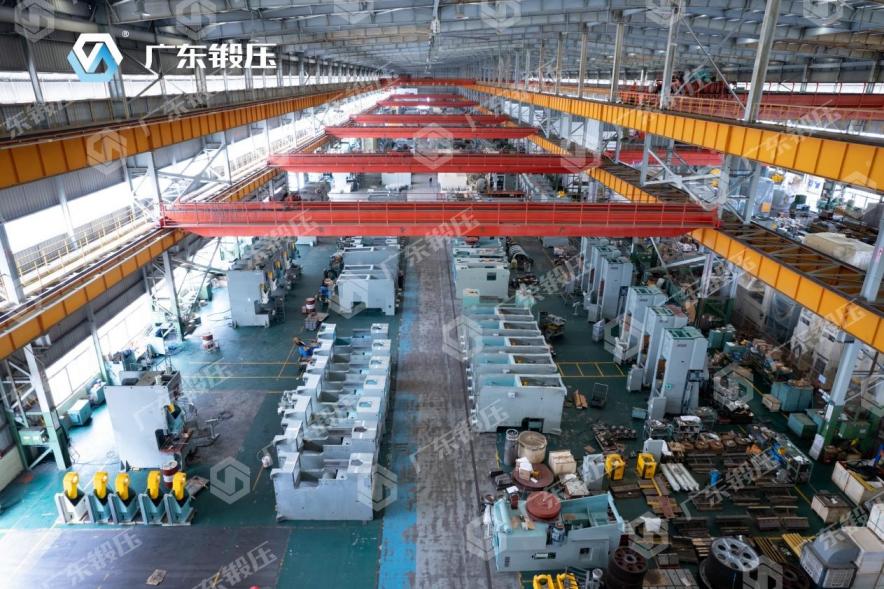
Advantages of Using Knuckle Joint Press Punch Machines
In a manufacturing world where precision and speed are critical to remaining competitive, the Knuckle Joint Press Punch Machine GK Series offers several key advantages that distinguish it from other punch machines available in the market.
Precision and Control at Its Best
One of the principal benefits of the GK series lies in its exceptional precision. This is largely attributed to the die height indicator, with its 0.01mm accuracy display, ensuring that the machine consistently produces components with minimal deviations from the desired specifications. Such high levels of accuracy are crucial in industries such as aerospace and electronics, where even the smallest of flaws could lead to product failure or significant safety concerns.
Enhanced Efficiency in High-Volume Production
Equipped with a pneumatic friction clutch brake system and the crank toggle mechanism, the GK series allows manufacturers to achieve fast and efficient production cycles without compromising on accuracy. This capability makes it a highly effective solution for large-scale production environments, where speed directly impacts profitability. Additionally, the dwell time at the bottom dead center enables the punch to exert maximum force, thereby increasing efficiency without reducing the machine’s operational longevity.
Versatility Across a Spectrum of Industries
Another strong suit of the GK series is its adaptability. This machine is designed to handle a variety of materials, from lightweight metals to heavy-duty alloys, allowing manufacturers to diversify their production lines. Whether it’s the creation of delicate electronic components or the forging of large automotive parts, the GK series can manage it all with ease and precision.
The Many Applications of the Knuckle Joint Press Punch Machine GK Series
Owing to its advanced design and multifaceted capabilities, the GK Series is utilized across a variety of industries, particularly in fine stamping and extrusion processes. Below are some of the key sectors benefiting from this technology.
Automotive Industry
In the automotive sector, which demands highly precise and durable components produced on a large scale, the GK series is an indispensable asset. Its high tonnage capacity makes it perfect for forming large metal components, while its precision ensures that all parts conform to stringent industry standards.
Electronics Industry
In the electronics domain, where components are often small and intricate, the GK series is especially valuable. Its capability to deliver precise measurements with an accuracy of 0.01mm guarantees that even the most delicate components are stamped correctly, minimizing the risk of defects that could compromise electronic circuits or assemblies.
Aerospace Industry
The aerospace industry sets extremely high standards for component manufacturing, where safety and performance are non-negotiable. The GK series excels in producing high-strength metal parts required for aircraft and spacecraft construction, thanks to its combination of precision and power. This ensures that manufacturers can meet the strict demands of the aerospace sector.
Conclusion: The Future of Manufacturing Lies in the Knuckle Joint Press Punch Machine GK Series
The Knuckle Joint Press Punch Machine GK Series from GUANGDUAN represents a pivotal advancement in the realm of precision stamping and forging technology. Its mix of high precision, versatile configurations, and robust performance make it an indispensable tool for manufacturers striving to streamline their production lines.
With the global trend leaning towards more efficient, cost-effective, and versatile manufacturing solutions, the GK series is well-positioned to address the growing demand for punch machines capable of handling the challenges posed by modern production processes. Whether used in the automotive, electronics, or aerospace industries, this machine provides the durability and accuracy required to remain competitive in today’s rapidly changing industrial landscape.
The future of manufacturing is unfolding now, and it is being driven by cutting-edge technologies such as the Knuckle Joint Press Punch Machine GK Series.
CONTACT US

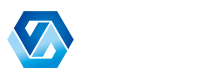
Guangdong Metal Forming Machine Works Co., Ltd.
We are always providing our customers with reliable products and considerate services.
If you would like to keep touch with us directly, please go to contact us