
What Are the Different Types of Dies Used with a Mechanical Stamping Press?
Mechanical stamping presses have revolutionized the manufacturing industry, providing businesses with the ability to shape, cut, and form metal with extreme precision. But what exactly makes these machines such an essential part of modern production? How do they work, and why are they so important in industries like automotive, electronics, and aerospace? In this blog, we will explore the different types of dies used with a mechanical stamping press, common troubleshooting techniques, the impact of automation, and much more.
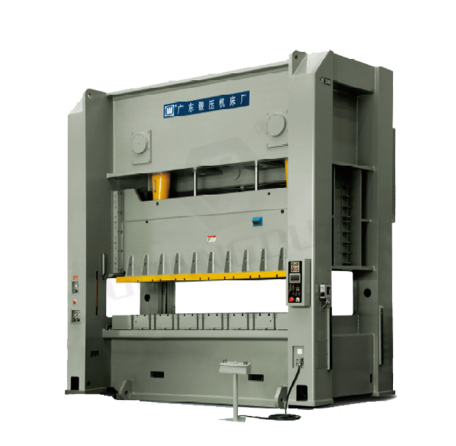
The Different Types of Dies Used with a Mechanical Stamping Press
What Are Dies and Why Are They Important?
A die is a specialized tool used in stamping presses to shape metal into a particular form. Dies play a crucial role in defining the shape and structure of stamped components, and they are typically made of high-strength tool steel to withstand the extreme pressures and temperatures involved in stamping processes.
Types of Dies in Mechanical Stamping Presses
Progressive Dies
Progressive dies are commonly used in mechanical stamping presses for high-volume production. These dies allow multiple operations to be performed in a single pass of the press. As the metal sheet moves through the die, it undergoes several processes, such as punching, bending, and forming. This makes progressive dies highly efficient and ideal for continuous manufacturing.
Compound Dies
Compound dies are designed to perform two or more operations on the material at once. These dies can cut, pierce, and form parts simultaneously, making them perfect for creating complex shapes in one stroke. This type of die is suitable for simple to moderately complex parts.
Single Operation Dies
As the name suggests, single operation dies perform one task at a time. This might include cutting, punching, or bending. Although not as efficient as progressive or compound dies, they are often used for simpler applications where precision is critical.
Transfer Dies
Transfer dies are used in situations where parts need to be moved between different stations in a stamping press. These dies are ideal for high-precision applications where multiple operations are required, and the part needs to be transferred through the press manually or automatically.
Troubleshooting Common Mechanical Stamping Press Issues
Identifying Common Problems
Mechanical stamping presses, like any heavy machinery, can encounter issues that affect performance. Understanding these problems can help manufacturers reduce downtime and keep production running smoothly. Some of the most common issues include:
Inconsistent Part Quality
This is often caused by issues such as die misalignment, worn-out dies, or improper machine setup. Consistency is crucial in stamping operations, and poor-quality parts can lead to costly rework and scrap.
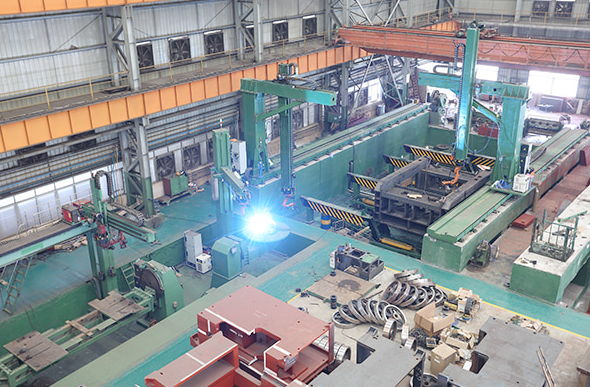
Machine Overload
If the mechanical stamping press is subjected to loads beyond its design limits, it can lead to overheating, breakdowns, and even permanent damage. Proper monitoring of load capacities and regular maintenance can help prevent such issues.
Sticking Dies
Dies that become sticky due to lubrication failure or improper material handling can cause jams and delays in production. Using the correct lubricants and ensuring regular cleaning of the dies can reduce the likelihood of this problem.
Noise and Vibration
Excessive noise or vibration is often a sign of misalignment or worn-out components. These issues can cause damage to the machine’s structural integrity and reduce its overall performance.
Troubleshooting Tips
Check Die Alignment: Misaligned dies can cause uneven pressure distribution and lead to part defects. Regularly check and adjust the alignment of the dies to maintain consistent part quality.
Monitor Lubrication: Inadequate lubrication can cause wear and tear on dies and machine components. Use the appropriate lubrication and ensure regular maintenance to keep the press running smoothly.
Inspect the Clutch and Brake System: Problems with the clutch and brake system can lead to irregular press operations. Regular checks and replacements can prevent malfunctioning and downtime.
Regular Maintenance: Schedule regular maintenance to clean, lubricate, and inspect key components of the press. This helps catch issues before they become serious problems.
Precision in Metalworking: The Importance of Mechanical Stamping Presses
Why Precision Matters in Stamping Operations
Precision is a defining characteristic of mechanical stamping presses. These machines must consistently deliver parts with tight tolerances to meet the requirements of modern manufacturing. Whether it’s the aerospace industry, where even a fraction of a millimeter can make a difference, or the automotive sector, where parts need to fit perfectly together, precision is essential.
Mechanical stamping presses, especially models like the Straight Side Double Point Multi Station Press GD2 from GUANGDUAN, offer unparalleled precision in metalworking. The key features contributing to this high level of precision include:
Eight-Surface Full-Guideway Guiding: This system minimizes side force and ensures the slide operates smoothly with little friction, thus enhancing the precision of each press stroke.
Unbalance Load Resistance: The design of the GD2 model includes an enlarged interval between the crank and connecting rod, giving the press increased resistance to unbalanced loads. This ensures that even when multiple dies are used in a multi-station setup, the machine maintains accuracy.
High-Quality Materials: The machine’s main structural components are made using superior-quality steel plates that are welded to provide excellent rigidity. This construction helps the press maintain its precision over long periods of operation.
Integrating Automation with Mechanical Stamping Presses
The Rise of Automation in Stamping Press Operations
As industries demand faster production rates and higher precision, automation has become a crucial aspect of mechanical stamping presses. Automated systems help streamline operations, reduce human error, and increase throughput. Mechanical presses, such as the GD2 model, can be integrated with automated systems to enhance performance.
Progressive Die Automation
Automated progressive die systems feed material automatically into the press, reducing the need for manual handling. This ensures higher throughput and less labor-intensive operation.
Multi-Station Automation
Multi-station presses are commonly used in combination with automated material handling systems. With these setups, parts can be automatically transferred from one station to the next without manual intervention, making the process highly efficient.
Servo Production Line Integration
The GD2 model comes with interfaces for both two-dimensional and three-dimensional servo production line installations. These systems improve overall automation, allowing for precise control over the entire stamping process.
Robotic Assistance
In some advanced setups, robotic arms are used to load and unload materials from the stamping press, making the process fully automated. This reduces the risk of human injury and speeds up production.
The Environmental Impact of Mechanical Stamping Press Operations
Minimizing the Environmental Footprint
Like many manufacturing processes, mechanical stamping can have environmental impacts. These include energy consumption, waste production, and noise pollution. However, advancements in press technology, such as those seen in the GD2 model from GUANGDUAN, are helping to mitigate these effects.
Energy Efficiency
Modern mechanical stamping presses are designed to be energy-efficient, with advanced clutch and braking systems that minimize power usage. The GD2 model, for example, features a high-torque wet-type clutch that consumes less energy and produces less noise compared to older systems.
Waste Reduction
With precise control over the stamping process, manufacturers can reduce material waste. The ability to produce parts with minimal scrap not only reduces the environmental footprint but also cuts production costs.
Noise Pollution
The GD2 press is designed with noise reduction in mind, featuring components that minimize vibration and noise, making it a more environmentally friendly option for high-volume stamping operations.
Why Choose GUANGDUAN for Your Mechanical Stamping Press Needs?
Trusted Quality and Expertise
GUANGDUAN, established in 1958, has over 65 years of experience in developing cutting-edge metal stamping technology. As the largest forging and press machine manufacturer in Southern China, GUANGDUAN is renowned for its commitment to quality and innovation.
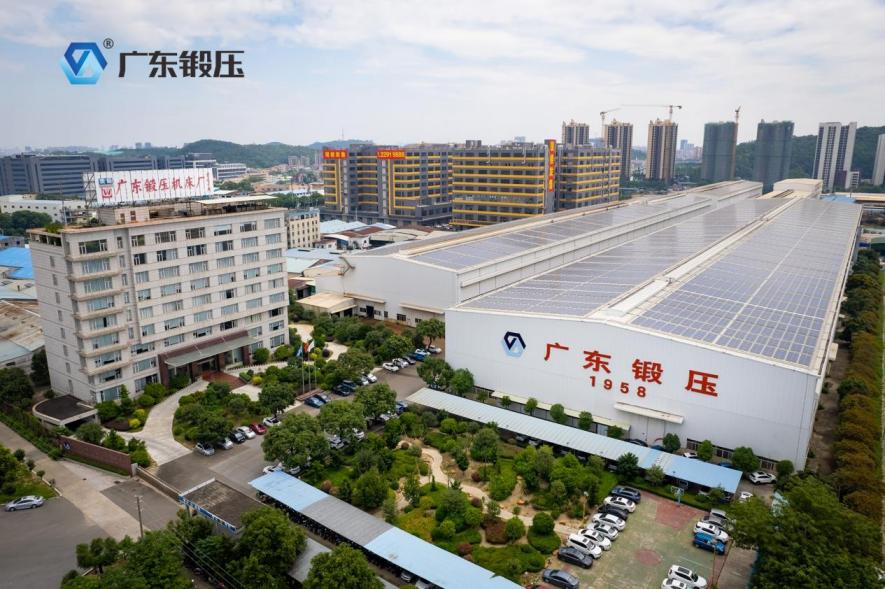
With a focus on producing reliable, high-precision mechanical presses, GUANGDUAN has earned a reputation as a national high-tech enterprise. The company offers a range of solutions, including hydraulic presses, mechanical presses, and forging presses, tailored to meet the needs of industries worldwide.
GUANGDUAN’s presses, like the Straight Side Double Point Multi Station Press GD2, incorporate advanced features such as high-torque wet-type clutches, multi-station capabilities, and precision-guided systems. Whether you are looking to increase throughput, reduce waste, or enhance part quality, GUANGDUAN is your trusted partner in mechanical stamping press solutions.
Conclusion
Mechanical stamping presses, such as those provided by GUANGDUAN, are essential tools for modern manufacturing. With the right dies, efficient troubleshooting methods, and a focus on precision, these machines can help businesses achieve high-quality production while minimizing costs and environmental impact. Whether you’re looking to integrate automation, improve operational efficiency, or choose the right press for your business, understanding the capabilities and features of mechanical stamping presses will help you make informed decisions that support long-term success.
CONTACT US

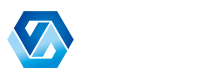
Guangdong Metal Forming Machine Works Co., Ltd.
We are always providing our customers with reliable products and considerate services.
If you would like to keep touch with us directly, please go to contact us