
What Are the Common Challenges with Mechanical Forging Presses and How to Overcome Them
Mechanical forging presses are widely used in the manufacturing sector for metal shaping and forming processes. However, like any industrial machine, they come with their own set of challenges. Understanding these challenges and knowing how to address them is key to ensuring optimal performance and longevity of your equipment. In this blog, we will explore the common issues faced by manufacturers using mechanical forging presses and provide solutions to overcome them.
Common Challenges with Mechanical Forging Presses
High Maintenance Costs Mechanical forging presses are heavy-duty machines subjected to intense wear and tear. This can lead to frequent maintenance requirements, particularly if the machine is not regularly maintained or operated within its specified parameters.
Precision Issues Over time, the precision of mechanical presses can degrade due to wear of components like slides, crankshafts, and die sets. This often leads to defects in the forged products, impacting quality and productivity.
Machine Downtime Mechanical presses that experience breakdowns or failures cause production downtime, which in turn affects overall output and profitability. Such issues are particularly troublesome when spare parts are not readily available or when repairs take longer than anticipated.
Energy Consumption Mechanical forging presses are energy-intensive, especially when operating at high speeds or under heavy loads. Over time, this can lead to high operational costs, particularly in industries with narrow profit margins.
Overcoming These Challenges
Regular Maintenance and Upgrades Implementing a comprehensive preventive maintenance schedule can reduce unexpected failures and minimize downtime. Regular inspections of key components, such as the crankshaft, guideways, and clutch system, are essential to identify potential issues before they cause significant damage.
Precision Calibration To address precision concerns, it’s vital to invest in high-quality mechanical presses like the JH25 Series Open-Back Double-Point Press, which is designed with a high-rigidity frame and precision-engineered components. These features ensure that the machine operates with a high degree of accuracy, reducing the risk of defects in the final product.
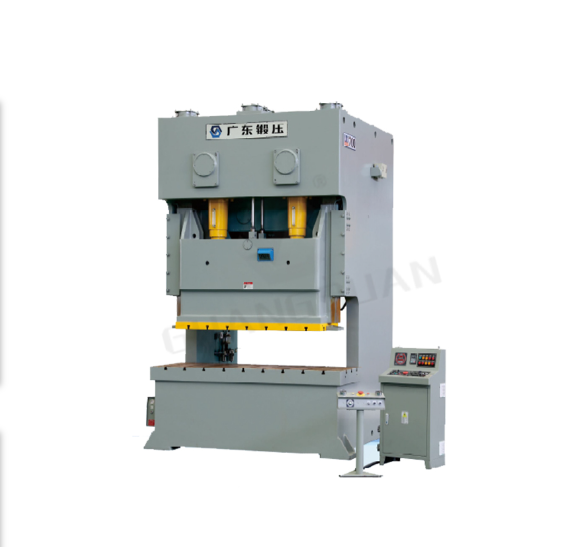
Investing in Spare Parts and Training Having access to reliable spare parts and a well-trained workforce is crucial for minimizing downtime. Regular training on troubleshooting and repair can ensure that employees are prepared to quickly address any issues that arise during operation.
Energy-Efficient Models Newer mechanical press models are designed with energy efficiency in mind. Investing in machines with lower energy consumption can help reduce operational costs over time. Additionally, integrating automation and advanced control systems, such as PLC systems, can further enhance energy efficiency.
How to Choose the Right Mechanical Forging Press for Your Manufacturing Needs
Choosing the right mechanical forging press is crucial for the success of any metalworking operation. The machine you select will have a direct impact on the quality of your products, production speed, and operational costs. In this section, we will guide you through the key factors to consider when choosing a mechanical forging press.
Key Factors to Consider
Type of Press There are various types of mechanical forging presses, each suited to specific applications. The Open-Back Double-Point Press, like the JH25 Series, is ideal for heavy-duty forging applications where high rigidity and precision are required. On the other hand, the Closed-Type Single-Point Press, like the JH31 Series, is well-suited for smaller, more precise applications, offering improved bearing capacity and longevity.
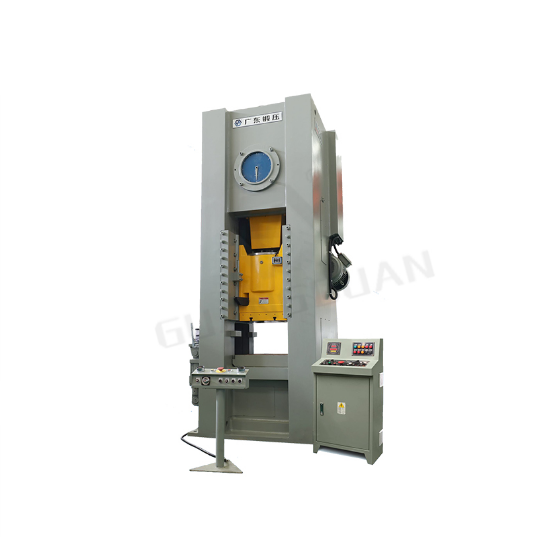
Machine Capacity and Size When choosing a mechanical press, it’s essential to match the machine’s capacity with the scale of your production. Consider factors like the size and weight of the parts you are forging, as well as the desired production speed. Ensure that the press you choose can handle the specific tonnage and stroke lengths required for your operations.
Precision and Control Precision is critical in forging operations. Presses like the JH25 Series Open-Back Double-Point Press offer high-precision die adjustments with a 0.1mm tolerance, ensuring accurate and consistent results. Look for presses that come with advanced control systems like PLC and pneumatic controls, which can optimize precision and improve overall efficiency.
Automation Compatibility As manufacturing processes become increasingly automated, selecting a forging press that can integrate with automated production lines is becoming essential. The JH25 Series, for example, can be linked with uncoiling and leveling devices, allowing for fully automated stamping processes. This integration helps reduce manual labor, improve consistency, and speed up production.
Understanding the Different Types of Mechanical Forging Presses: Which One Is Right for You?
Mechanical forging presses come in various configurations and sizes to suit different production needs. Two of the most common types are the Open-Back Double-Point Press and the Closed-Type Single-Point Press. Understanding the differences between these types can help you choose the right one for your manufacturing requirements.
Open-Back Double-Point Press (JH25 Series)
The Open-Back Double-Point Press is a robust machine designed for heavy-duty forging tasks. This machine features a high-rigidity frame and a symmetrical design to ensure the stability and accuracy of its operations.
Key Features:
1. High-rigidity frame for improved stability
2. Double crankshafts designed to counteract side forces
3. Precision die adjustment (up to 0.1mm)
4. Pneumatic wet-type friction clutch for lower noise and longer lifespan
5. Hydraulic overload protection for improved safety
The JH25 Series is ideal for heavy, high-volume forging applications that require both precision and durability. This machine is commonly used in automotive, aerospace, and other industries that require strong, reliable metal forming.
Closed-Type Single-Point Press (JH31 Series)
The Closed-Type Single-Point Press, like the JH31 Series, is designed with a more compact structure and is suitable for applications where precision is paramount. It is especially effective in high-speed production environments, where consistent quality is crucial.
Key Features:
1. Strong bearing capacity with eccentric crankshaft
2. Wet-type clutch for extended service life
3. Four-surface full-guideway for precise motion control
4. Hydraulic overload protection device
5. PLC and pneumatic control modes for versatile operation
The JH31 Series is ideal for industries like electronics, instrumentation, and small metal parts production, where smaller parts with high precision are produced.
How to Troubleshoot Common Issues in Mechanical Forging Press Machines
Mechanical forging presses, like any piece of heavy machinery, can experience issues over time. Understanding how to troubleshoot common problems can help you address issues quickly and minimize downtime.
Common Issues and Their Solutions
Inconsistent Product Quality If the forged parts are inconsistent in shape or size, the issue could lie in the die setup, machine alignment, or wear in key components. Ensure the die is properly adjusted, and regularly check the machine’s alignment. For precision presses like the JH25 Series, check the die adjustment and perform regular maintenance to keep the machine running smoothly.
Unusual Vibrations Excessive vibrations during operation may indicate issues with the machine’s foundation, crankshaft, or bearings. It’s essential to check the stability of the machine’s foundation and ensure that all critical components are well-lubricated and functioning properly.
Hydraulic System Failure If you experience problems with the hydraulic system, such as poor responsiveness or leaks, inspect the hydraulic fluid levels, hoses, and pumps. For models such as JH31 series. Make sure the hydraulic overload protection system operates normally to avoid machine damage.
The Future of Mechanical Forging Presses: Innovations and Trends to Watch
The mechanical forging press industry is undergoing rapid innovation. As manufacturing demands evolve, new technologies and trends are shaping the future of these machines. Here’s what you can expect in the years to come.
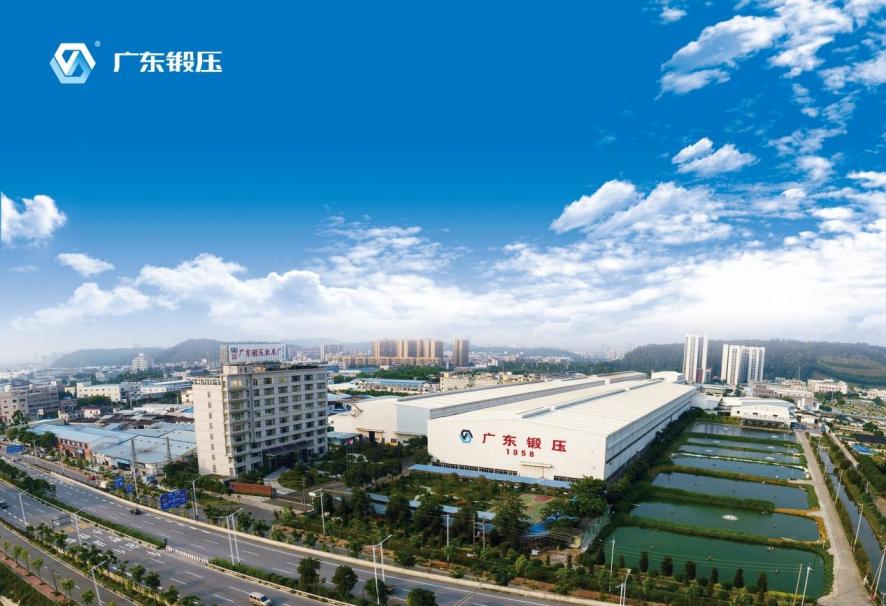
Key Innovations
Automation Integration Increasing automation in the manufacturing industry will lead to more fully automated forging presses. These presses will integrate seamlessly with robotic systems, material handling equipment, and automated inspection systems, creating smarter and more efficient production lines.
Energy-Efficiency and Sustainability Future mechanical forging presses will be designed with even more energy-efficient features to reduce operational costs and environmental impact. Look for presses with advanced motor control systems and energy recovery mechanisms.
AI and Predictive Maintenance The rise of artificial intelligence (AI) and machine learning will transform how mechanical presses are maintained. Predictive maintenance algorithms will help monitor machine health and forecast potential failures, allowing manufacturers to address issues before they lead to breakdowns.
Conclusion
Mechanical forging presses remain a cornerstone of modern manufacturing, offering precision, durability, and efficiency. By understanding the common challenges, selecting the right press, troubleshooting effectively, and staying abreast of innovations, manufacturers can optimize their forging operations. Companies like GUANGDUAN, with decades of expertise and cutting-edge technology, offer top-of-the-line mechanical presses designed to meet the demands of the future. Whether you’re forging heavy-duty parts or producing high-precision components, the right machine and maintenance strategies are essential for success.
CONTACT US

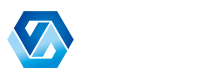
Guangdong Metal Forming Machine Works Co., Ltd.
We are always providing our customers with reliable products and considerate services.
If you would like to keep touch with us directly, please go to contact us