
What Impact Do Industrial Stamping Presses Have on Global Manufacturing?
Explore the precision, efficiency, and cost-effectiveness of industrial stamping presses. Delve into their pivotal role in manufacturing, essential safety considerations, and upcoming innovations. Unlock the advantages with GUANGDUAN, a renowned leader in stamping press manufacturing.
Introduction to Industrial Stamping Presses
1.1 Definition and Significance
Industrial stamping presses are vital machines in the manufacturing sector, used to shape and form metal sheets into various components with high precision and efficiency. Their significance in manufacturing cannot be overstated, as they play a crucial role in producing a wide range of products across diverse industries. From automotive parts to electronic components, industrial stamping presses are instrumental in shaping the modern world of manufacturing.
1.2 History and Evolution
The history of industrial stamping presses dates back to the late 18th century when the first mechanical presses were developed. Over the years, these machines have undergone significant evolution, incorporating advancements in technology and engineering principles. From manual operation to automated systems, the evolution of stamping presses has revolutionized the manufacturing industry, enabling faster production rates and higher precision.
1.3 Role in Various Industries
Industrial stamping presses find applications in various industries, including automotive, aerospace, electronics, and consumer goods. In the automotive sector, stamping presses are used to manufacture body panels, chassis components, and structural parts with exceptional accuracy and consistency. Similarly, in the aerospace industry, these machines are employed to produce intricate parts for aircraft and spacecraft, meeting stringent quality standards. Moreover, in the electronics industry, stamping presses play a vital role in manufacturing circuit boards, connectors, and other electronic components.
Types of Industrial Stamping Presses
2.1 Mechanical Stamping Presses
Mechanical stamping presses utilize mechanical energy to perform the stamping process. They are known for their simplicity, reliability, and high-speed operation. Mechanical presses are commonly used in industries where high production volumes and fast cycle times are required, such as automotive and appliance manufacturing.
2.2 Hydraulic Stamping Presses
Hydraulic stamping presses utilize hydraulic power to exert force on the workpiece, allowing for precise control over the stamping process. These presses are favored for their versatility and ability to generate high forces at low speeds. Hydraulic presses are commonly used in industries where forming thicker materials or performing deep drawing operations is required, such as shipbuilding and heavy equipment manufacturing.
2.3 Servo-Driven Stamping Presses
Servo-driven stamping presses incorporate servo motors to drive the ram or slide, offering precise control over stroke length, speed, and force. These presses are highly efficient and energy-saving, as they only consume power when in use. Servo-driven presses are ideal for applications requiring complex forming processes, tight tolerances, and flexibility in production, such as precision metal stamping and electronics manufacturing.
Key Components and Working Mechanism
3.1 Main Components
Industrial stamping presses consist of several main components, including the frame, bed, slide, and die. The frame provides structural support and houses the other components of the press. The bed serves as the base on which the workpiece rests during the stamping process. The slide, or ram, is the moving component that applies force to the workpiece. The die is a specialized tool that shapes the workpiece according to the desired geometry.
3.2 Working Mechanism
During operation, the workpiece is placed on the bed of the press, and the die is positioned above it. As the slide moves downward, the die applies force to the workpiece, causing it to deform and take the shape of the die cavity. The force applied by the slide is controlled by the press’s hydraulic or mechanical system, ensuring precise forming of the workpiece. Once the desired shape is achieved, the slide retracts, and the stamped part is removed from the press.
Benefits of Industrial Stamping Presses
4.1 High Precision and Accuracy
Industrial stamping presses offer unparalleled precision and accuracy in shaping metal components. With precise control over force and speed, these machines can produce parts with tight tolerances, ensuring consistency and quality in manufacturing processes. Whether it’s automotive body panels or electronic components, stamping presses deliver precise results that meet the most stringent specifications.
4.2 Rapid Production
One of the key benefits of using stamping presses in manufacturing is their ability to achieve rapid production rates. These machines can perform multiple stamping operations in quick succession, allowing manufacturers to meet high demand and tight production schedules. Whether it’s mass-producing automotive parts or consumer goods, stamping presses excel in high-volume production environments, maximizing efficiency and throughput.
4.3 Cost-Effectiveness
Stamping presses offer cost-effective solutions for manufacturing metal components compared to alternative methods such as machining or casting. By utilizing efficient processes and minimizing material waste, stamping presses help reduce production costs and improve overall profitability. Additionally, their ability to produce complex shapes in a single operation further enhances cost-effectiveness by streamlining production processes and reducing labor and tooling costs.
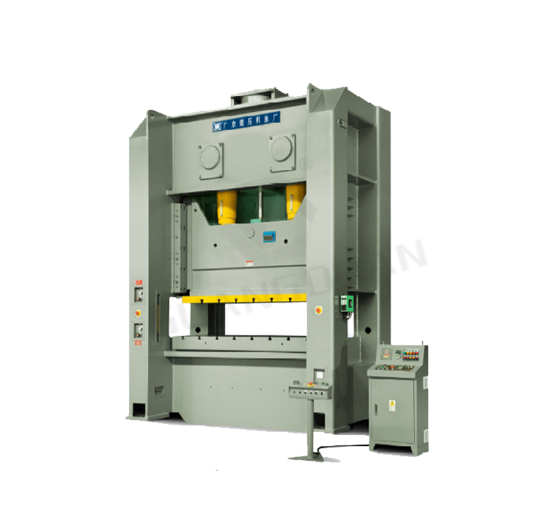
4.4 Case Studies and Testimonials
Numerous companies across various industries have benefited from the advantages of industrial stamping presses. For example, a leading automotive manufacturer increased production efficiency by 30% after implementing stamping presses in their manufacturing facility. Similarly, a consumer electronics company achieved significant cost savings by transitioning to stamping processes for producing intricate metal components. These success stories highlight the tangible benefits that stamping presses bring to manufacturing operations.
Safety Considerations and Regulations
5.1 Importance of Safety
Safety is paramount when operating industrial stamping presses due to the inherent risks associated with high-force machinery. Operators must adhere to strict safety protocols to prevent accidents and injuries in the workplace. Proper training, maintenance, and supervision are essential to ensure the safe operation of stamping presses and protect the well-being of workers.
5.2 Common Hazards and Risks
Common safety hazards associated with stamping presses include crush injuries, entanglement, and ejection of workpieces or tooling. Operators must be vigilant when working around these machines and follow safety guidelines to minimize the risk of accidents. Additionally, improper maintenance or use of faulty equipment can lead to mechanical failures, posing serious safety threats to operators and bystanders.
5.3 Regulations and Guidelines
Manufacturers are required to adhere to safety regulations and guidelines set forth by regulatory bodies such as OSHA (Occupational Safety and Health Administration) to ensure compliance with safety standards. These regulations outline specific safety measures and requirements for operating stamping presses, including machine guarding, lockout/tagout procedures, and employee training. By following these regulations, manufacturers can create safer work environments and mitigate the risk of workplace accidents.
Future Trends and Innovations
6.1 Advancements in Automation and Robotics
The future of industrial stamping presses lies in automation and robotics, enabling enhanced productivity, flexibility, and efficiency in manufacturing operations. Advanced robotic systems integrated with stamping presses can perform intricate tasks with precision and consistency, reducing the need for manual intervention and increasing overall throughput. Additionally, automation technologies such as vision systems and artificial intelligence are revolutionizing stamping processes by optimizing tooling setups, detecting defects, and improving quality control.
6.2 Digitalization and Smart Manufacturing
Digitalization is transforming the manufacturing industry, and stamping presses are no exception. Digital technologies such as IoT (Internet of Things) sensors and data analytics provide real-time insights into machine performance, enabling predictive maintenance and optimizing production processes. Smart manufacturing systems interconnected with stamping presses can monitor production parameters, track inventory levels, and adapt to changing demand, ensuring seamless operations and maximizing efficiency.
6.3 Impact on the Future of Manufacturing
The advancements in stamping press technology are poised to reshape the future of manufacturing by driving innovation, agility, and sustainability. With automation, robotics, and digitalization at the forefront, manufacturers can achieve higher levels of productivity, quality, and cost-effectiveness in metal forming processes. Furthermore, these advancements enable manufacturers to respond quickly to market demands, customize products on demand, and reduce environmental impact through efficient resource utilization and waste reduction.
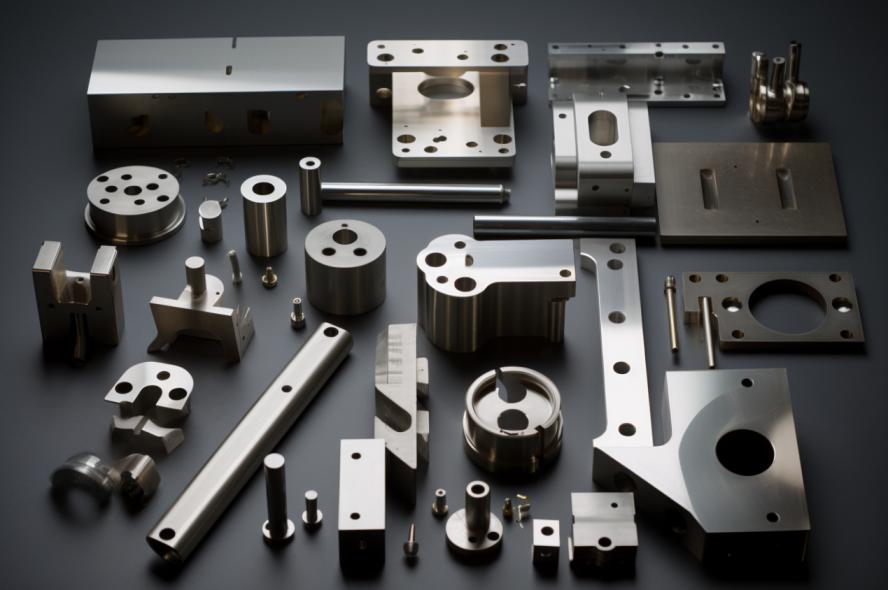
Conclusion
In conclusion, industrial stamping presses are indispensable machines in the manufacturing industry, offering high precision, efficiency, and versatility in shaping metal components. With various types available, including mechanical, hydraulic, and servo-driven presses, manufacturers can choose the right equipment for their specific applications. As technology continues to advance, the role of stamping presses in manufacturing will only become more critical, driving innovation and progress in various industries.
CONTACT US

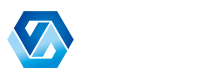
Guangdong Metal Forming Machine Works Co., Ltd.
We are always providing our customers with reliable products and considerate services.
If you would like to keep touch with us directly, please go to contact us