
GUANGDUAN’s Hydraulic Metal Forming Press Solutions: Revolutionizing Metal Forming
The metal forming industry is the backbone of manufacturing, enabling the production of a wide array of components across various sectors such as automotive and construction. Despite its significance, the industry faces numerous challenges that impede efficiency, quality, and overall productivity. This blog delves into the critical issues faced by the metal forming industry and explores how GUANGDUAN’s hydraulic metal forming press offers innovative solutions to address these challenges.
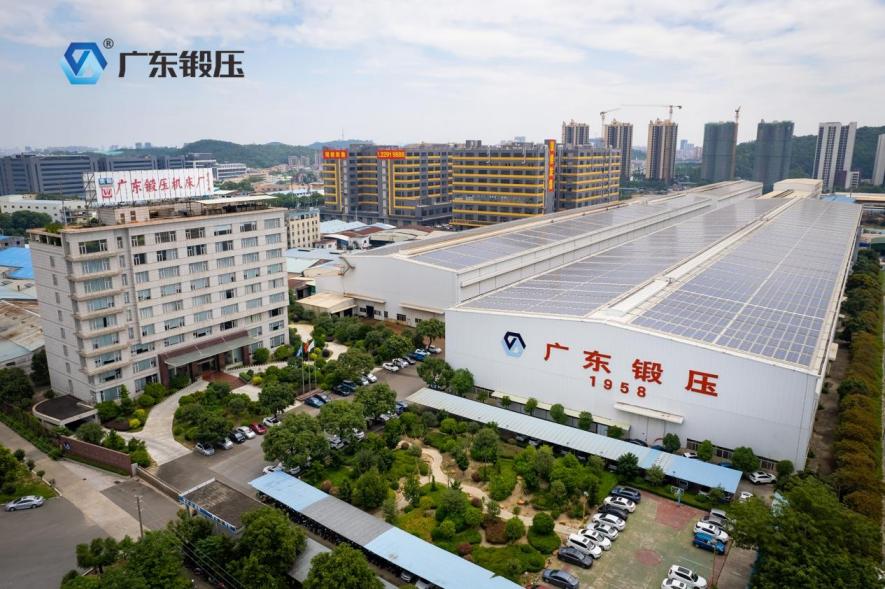
Challenges in the Metal Forming Industry
1.1 Quality Control Issues
Inconsistent Material Properties
One of the primary challenges in metal forming is dealing with inconsistent material properties. Variations in the composition, thickness, and hardness of metal sheets can lead to unpredictable outcomes during forming, resulting in defects such as cracks, wrinkles, and springback. These inconsistencies necessitate rigorous quality control measures, increasing both the cost and time required for production.
Surface Defects
Surface defects such as scratches, dents, and tool marks are common issues in metal forming. These defects not only compromise the aesthetic appeal of the final product but also affect its functional integrity. Ensuring a defect-free surface requires precision in both the tooling and forming processes, which can be difficult to achieve with traditional methods.
Dimensional Accuracy
Achieving precise dimensions is crucial for components that must fit together seamlessly. Variations in temperature, pressure, and material properties can all contribute to dimensional inaccuracies. Maintaining tight tolerances is essential, particularly in industries where even minor deviations can lead to significant performance issues.
1.2 Operational Efficiency
High Energy Consumption
Metal forming processes are energy-intensive, leading to high operational costs. Traditional mechanical presses often consume large amounts of electricity, contributing to both economic and environmental concerns. Reducing energy consumption while maintaining productivity is a significant challenge for manufacturers.
Slow Production Rates
The speed of production is a critical factor in meeting market demands. Traditional forming methods often involve multiple steps and long cycle times, resulting in slower production rates. This inefficiency can be a major bottleneck, especially when dealing with large volumes or complex components.
Tool Wear and Maintenance
The wear and tear of forming tools is a persistent issue that affects both the quality and cost-effectiveness of production. Frequent maintenance and replacement of tools can lead to downtime and increased operational costs. Enhancing tool life and minimizing maintenance requirements are essential for improving overall efficiency.
1.3 Technological Adaptation
Integration with Modern Manufacturing Systems
The metal forming industry is increasingly integrating with advanced manufacturing systems such as computer-aided design (CAD) and computer-aided manufacturing (CAM). Ensuring compatibility and seamless integration with these technologies is crucial for optimizing the forming process and enhancing productivity.
Automation and Robotics
Automation and robotics are transforming the manufacturing landscape, offering opportunities for increased efficiency and precision. However, integrating these technologies into traditional metal forming processes poses significant challenges, including the need for specialized equipment and skilled personnel.
Environmental and Safety Regulations
Compliance with stringent environmental and safety regulations is a major concern for metal forming industries. Reducing emissions, managing waste, and ensuring worker safety require significant investments in technology and processes, adding to the overall operational burden.
GUANGDUAN’s Hydraulic Metal Forming Press: A Solution-Oriented Approach
2.1 Advanced Quality Control
Precision Engineering
GUANGDUAN’s hydraulic metal forming presses are engineered for precision, addressing the issue of inconsistent material properties. The advanced control systems ensure uniform pressure distribution and accurate force application, minimizing defects and ensuring consistent quality across all components.
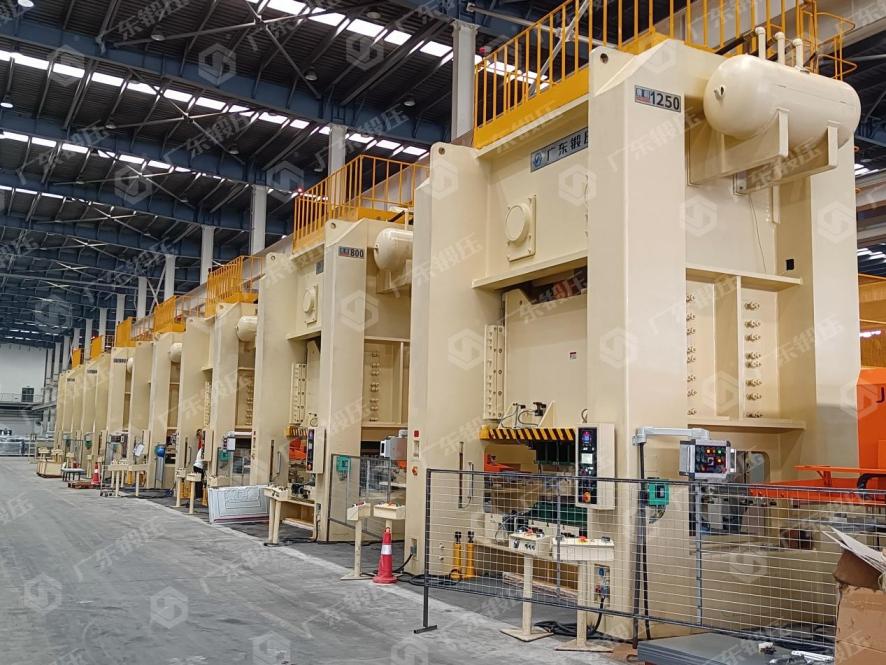
Superior Surface Finish
The hydraulic forming process employed by GUANGDUAN significantly reduces surface defects. The controlled application of pressure and the use of high-quality tooling result in smoother surfaces and fewer imperfections, enhancing both the aesthetic and functional qualities of the final products.
Tight Tolerances
GUANGDUAN’s presses are designed to achieve and maintain tight dimensional tolerances. The hydraulic system provides precise control over the forming process, reducing variability and ensuring that components meet exact specifications. This capability is particularly beneficial for industries requiring high precision, such as aerospace and automotive.
2.2 Enhanced Operational Efficiency
Energy-Efficient Design
GUANGDUAN’s hydraulic metal forming presses are built with energy efficiency in mind. The use of advanced hydraulic systems reduces energy consumption compared to traditional mechanical presses, lowering operational costs and contributing to a more sustainable manufacturing process.
High Production Rates
The hydraulic presses from GUANGDUAN are capable of achieving faster production rates through optimized cycle times and streamlined processes. The ability to quickly switch between different forming operations without extensive retooling further enhances productivity, making it possible to meet high-volume demands with ease.
Durability and Low Maintenance
The robust construction and high-quality materials used in GUANGDUAN’s hydraulic presses result in longer tool life and reduced maintenance requirements. This durability not only lowers operational costs but also minimizes downtime, ensuring continuous production and higher overall efficiency.
2.3 Integration with Modern Technology
Compatibility with CAD/CAM Systems
GUANGDUAN’s hydraulic metal forming presses are designed for seamless integration with modern CAD/CAM systems. This compatibility allows for precise control over the forming process, from design to execution, enhancing accuracy and reducing the time required for setup and adjustments.
Automation and Robotics Integration
The presses are equipped to integrate with advanced automation and robotics systems, enabling fully automated production lines. This integration reduces the need for manual intervention, increases production speed, and enhances precision, making it possible to achieve higher levels of efficiency and consistency.
Compliance with Regulations
GUANGDUAN’s hydraulic presses are designed to meet stringent environmental and safety standards. The energy-efficient operation, reduced emissions, and advanced safety features ensure compliance with regulations, providing peace of mind for manufacturers and contributing to a safer and more sustainable workplace.
Case Studies: Real-World Applications of GUANGDUAN’s Hydraulic Metal Forming Press
3.1 Automotive Industry
High-Volume Production
In the automotive industry, the demand for high-volume production of complex components is ever-present. GUANGDUAN’s hydraulic presses have been instrumental in enabling manufacturers to meet these demands by providing fast cycle times and consistent quality. The ability to maintain tight tolerances ensures that parts fit together seamlessly, reducing assembly time and improving overall vehicle quality.
Lightweight Material Forming
With the push towards more fuel-efficient vehicles, the use of lightweight materials such as aluminum and high-strength steel has become more common. GUANGDUAN’s hydraulic presses are capable of effectively forming these materials, ensuring that the components maintain their structural integrity while meeting the required specifications.
3.2 Consumer Electronics
Miniaturization and Precision
In the consumer electronics industry, the trend towards miniaturization requires the production of extremely precise and small components. GUANGDUAN’s hydraulic presses are well-suited for this task, providing the necessary control and accuracy to produce tiny, intricate parts used in electronic devices.
High-Quality Surface Finishes
The aesthetic appeal of consumer electronics is crucial, and surface defects are unacceptable. The hydraulic forming process used by GUANGDUAN ensures high-quality surface finishes, enhancing the visual and functional quality of electronic components and housings.
Conclusion
The metal forming industry faces a multitude of challenges, from maintaining quality control to improving operational efficiency and integrating with modern technologies. GUANGDUAN’s hydraulic metal forming presses offer comprehensive solutions to these challenges, providing precision, durability, and energy efficiency. By addressing the specific needs of various industries, from automotive to aerospace and consumer electronics, GUANGDUAN’s presses are revolutionizing metal forming processes and setting new standards for quality and efficiency. As the industry continues to evolve, GUANGDUAN remains at the forefront, driving innovation and helping manufacturers meet the demands of an increasingly complex and competitive market.
CONTACT US

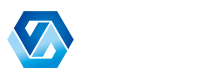
Guangdong Metal Forming Machine Works Co., Ltd.
We are always providing our customers with reliable products and considerate services.
If you would like to keep touch with us directly, please go to contact us