
What Are Hydraulic Forging Presses and How Do They Revolutionize Metal Forming?
Hydraulic forging presses have transformed the way industries approach metal forming. These advanced machines use hydraulic power to generate the high force necessary for shaping and forging metals, providing a level of precision and control that was previously unattainable with traditional methods.
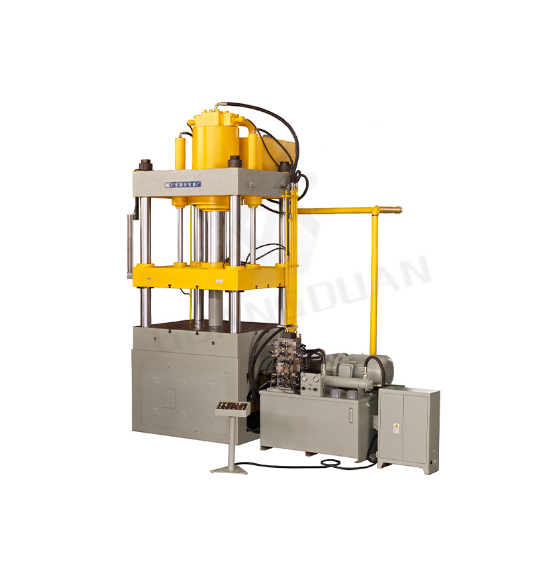
Hydraulic Forging Presses: An Introduction to Technology
A hydraulic forging press operates by using hydraulic fluid to transmit pressure to a piston or ram, which is then used to shape metal parts. Unlike mechanical presses, which rely on springs and mechanical linkages, hydraulic presses are powered by the controlled flow of hydraulic oil. This allows for much smoother operation and better control over the pressure applied. They are particularly useful for operations requiring precise, high-force applications like deep drawing, metal forging, and shaping complex parts.
The real revolution brought by hydraulic forging presses lies in their ability to precisely control the pressure and force applied to the material. This makes them perfect for industries requiring extremely accurate results, such as aerospace, automotive, and metalworking. By utilizing hydraulic power, these presses enable manufacturers to create parts with high strength, fine tolerances, and excellent surface finishes.
The Impact of Hydraulic Forging Presses on Manufacturing
One of the biggest advantages of hydraulic forging presses is the ability to handle high-tonnage work. Hydraulic presses can generate much higher pressures than traditional mechanical presses, allowing for the production of larger and more complex parts. This opens up new possibilities in industries that require large forged components, such as the aerospace and automotive sectors. Moreover, hydraulic presses are better suited for working with hard-to-machine materials, such as high-strength alloys and composites, that would be difficult or impossible to forge using older techniques.
Furthermore, the ability to program and control the speed, pressure, and movement of the press allows manufacturers to achieve consistent results, reduce scrap rates, and improve overall product quality. In an industry where efficiency and precision are paramount, hydraulic forging presses have become a game-changer.
How to Choose the Right Hydraulic Forging Press for Your Business Needs
Choosing the right hydraulic forging press for your operation is critical to ensuring optimal productivity, efficiency, and safety. Several factors must be taken into consideration when selecting a press that meets your specific requirements.
Factors to Consider When Selecting a Hydraulic Forging Press
When choosing a hydraulic forging press, it’s essential to consider the tonnage or force capacity of the machine. Tonnage is one of the primary specifications that determine what types of materials and parts can be forged using the press. Larger parts or harder materials will require a press with higher tonnage, while lighter, more delicate components may only require a machine with lower tonnage.
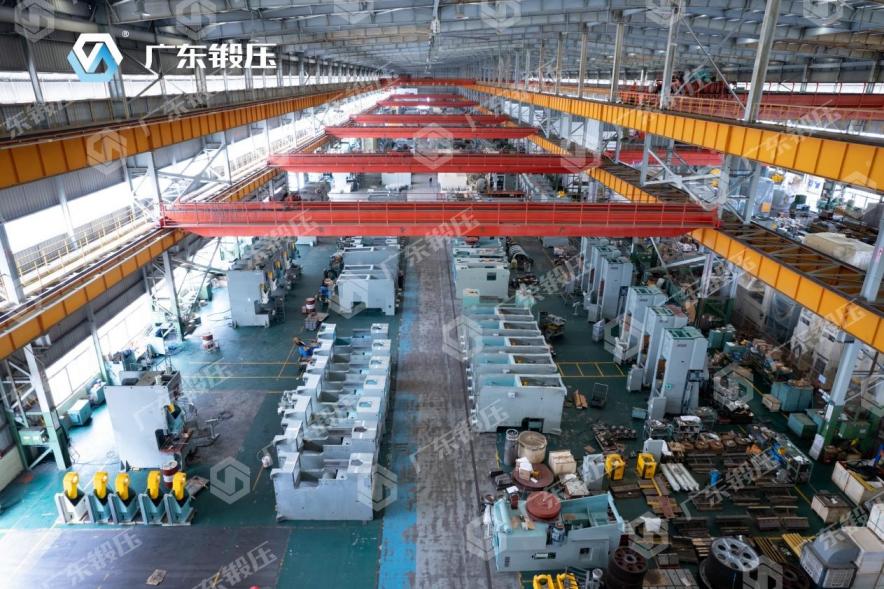
Another key consideration is the stroke length of the press. The stroke length refers to the distance the ram travels, and it should be chosen based on the size and shape of the parts you intend to forge. Some applications may require long strokes for deeper forming or to accommodate larger workpieces, while others may only require shorter strokes for smaller components.
Additionally, the speed and precision of the machine should be considered. Modern hydraulic presses allow for variable speed control, which is useful in optimizing the forging process for different materials and operations. Precision is critical for producing high-quality parts, and machines with advanced controls allow operators to set specific pressure and timing for each step of the forging process.
Hydraulic Press Features for Modern Manufacturers
When selecting a hydraulic forging press, look for one with adjustable pressure and stroke length to accommodate a variety of materials and parts. Many modern presses come with centralized button controls, which offer operators ease of use and the ability to adjust settings quickly. Another important feature is the ability to operate in both fixed pressure and fixed position modes, giving operators flexibility depending on the complexity of the parts being forged.
Safety is another critical consideration. Advanced presses are equipped with multiple safety features, including synchronized two-hand operation and anti-two-hand duplication safety functions. These measures help ensure the safety of operators while also improving productivity by minimizing downtime due to safety concerns.
The Future of Manufacturing: How Hydraulic Forging Presses Are Changing the Industry
Hydraulic forging presses are not just advancing in terms of technology; they are also playing a crucial role in shaping the future of manufacturing. These machines are helping to drive automation, reduce production costs, and improve the overall sustainability of metalworking operations.
Automation and Efficiency in Forging
The trend towards automation in manufacturing is rapidly gaining momentum, and hydraulic forging presses are at the forefront of this shift. With the integration of smart controls and sensors, modern hydraulic presses can automatically adjust pressure, stroke, and speed to optimize the forging process in real-time. This results in higher productivity, more consistent quality, and lower labor costs, all of which contribute to more competitive manufacturing processes.
In addition to automation, the ability to integrate hydraulic forging presses with other automated systems is revolutionizing the manufacturing industry. For example, presses can now be linked to material handling systems, quality control sensors, and computer-aided design (CAD) software, allowing for fully integrated production lines that require minimal human intervention. This is pushing the boundaries of what’s possible in terms of production speed, part complexity, and customization.
Sustainability and Reduced Waste
Hydraulic forging presses are also helping to address some of the environmental challenges facing the manufacturing industry. By offering better control over the forging process, these presses reduce the amount of material waste generated during production. Additionally, they can be used to produce parts with more precise geometries, reducing the need for additional machining or rework, which further cuts down on waste.
As manufacturers continue to seek more sustainable practices, hydraulic presses offer a path to achieving these goals. Their efficiency and precision help reduce energy consumption, minimize waste, and ultimately contribute to a more sustainable manufacturing environment.
Four Column Double Action Hydraulic Press Machine YA28 Series
The YA28 series is a popular model of four-column double action hydraulic presses, designed for high precision and versatility in metal forming. It is widely used for applications such as thin plate deep drawing, forming, aligning, bending, and folding. Industries like hardware manufacturing, appliance production, stainless steel ware, electronics components, and motor manufacturing rely heavily on this type of press.
Key Features of the YA28 Series
The YA28 series is designed with a four-column and three-beam structure, making it highly rigid and offering excellent guidance performance. This ensures smooth operation, even during high-load applications. One of the standout features of the YA28 series is its ability to provide fast idle running, improving overall efficiency.
The machine also comes with chrome-plated cylinders and rods, which undergo thermal refining and polishing for added durability and resistance to wear. These components contribute to the press’s long lifespan, making it a reliable investment for any manufacturer.
How the YA28 Series Works
In the YA28 series, the hydraulic system is composed of an integrated oil pump, control mechanisms, and an actuator that moves the cylinder. The oil pump delivers hydraulic fluid to a cartridge valve block, which then directs the fluid to the upper or lower chamber of the cylinder. By using the hydraulic principle of Pascal’s law, the machine applies pressure uniformly to shape the material.
The press is designed to accommodate different working modes, including fixed-position and fixed-pressure modes. These options allow manufacturers to select the best parameters for their specific needs, whether it’s precision forming or high-volume production.
Hydraulic Forging Presses Supplier: GUANGDUAN
Founded in 1958, GUANGDUAN is a leading supplier of hydraulic forging presses, known for its cutting-edge technology and extensive experience in the metal stamping industry. With over 65 years of development, GUANGDUAN has established itself as the largest forging and press machine manufacturer in Southern China.
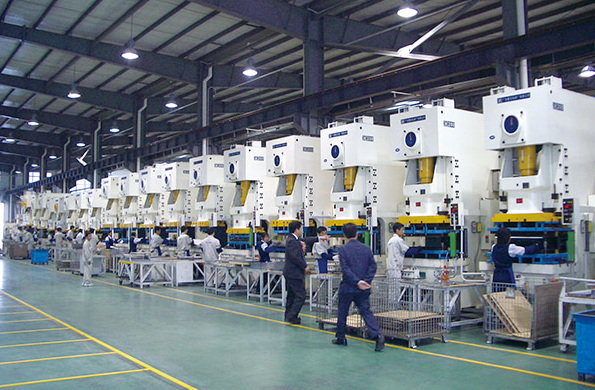
A History of Excellence
GUANGDUAN’s commitment to innovation has earned it a reputation for high-quality manufacturing and customer satisfaction. As a national high-tech enterprise, GUANGDUAN integrates research and development, manufacturing, and service to deliver state-of-the-art hydraulic press machines and solutions. The company’s expertise spans hydraulic, mechanical, and forging presses, and its machines are widely used across industries such as aerospace, automotive, and metalworking.
Meeting the Demands of the Industry
With over 800 skilled employees and a comprehensive array of advanced processing and inspection equipment, GUANGDUAN continues to push the boundaries of press machine technology. The company’s focus on customer service and satisfaction has made it a trusted partner for manufacturers worldwide. Whether you need a hydraulic forging press for small-scale operations or large-scale production, GUANGDUAN has the expertise and technology to meet your needs.
Conclusion
Hydraulic forging presses have revolutionized the metal forming industry by providing precise control, high tonnage capabilities, and versatility across a wide range of applications. As the industry continues to evolve, these presses are playing a critical role in advancing manufacturing techniques, boosting efficiency, and reducing waste. Whether you’re looking to upgrade your existing equipment or are just starting to explore the benefits of hydraulic forging presses, understanding the technology and its applications is key to staying competitive in the modern manufacturing landscape.
GUANGDUAN’s experience and innovation in hydraulic press manufacturing position it as a leader in this field, helping businesses optimize their production processes and achieve their manufacturing goals.
CONTACT US

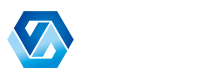
Guangdong Metal Forming Machine Works Co., Ltd.
We are always providing our customers with reliable products and considerate services.
If you would like to keep touch with us directly, please go to contact us