
How Does a Forge Press Work? Looke at Industrial Metal Forging
Imagine a machine so powerful it can shape solid steel like clay, crafting intricate components used in everything from automobiles to aerospace. The forge press is a marvel of modern engineering, providing precision and power to form metals into exact shapes. But how exactly does a forge press work, and what processes are involved in this transformation? In this article, we’ll break down the essentials of forge press mechanics, focusing on the How Does a Forge Press Work? And key stages in the forging process and the remarkable technology behind machines like the GUANGDUAN Knuckle Joint Press GK Series.
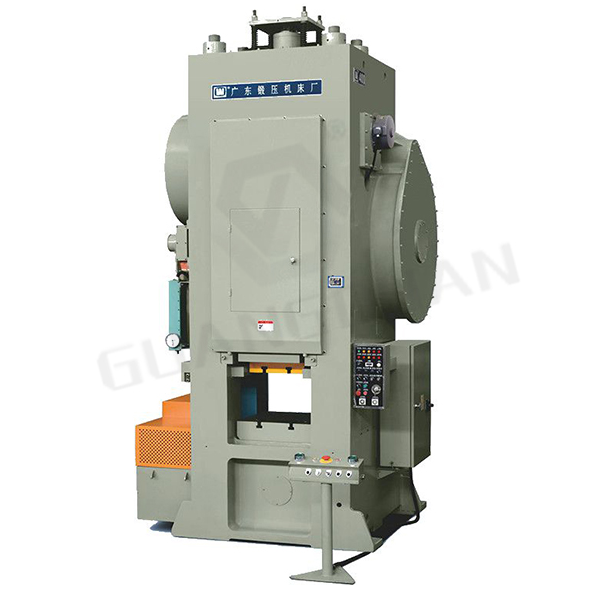
What Is a Forge Press, and Why Is It Important?
A forge press is an industrial machine used to shape metal through extreme force, heat, and pressure. Unlike other forming methods, forging doesn’t cut or grind down the metal but instead compresses it into a new form, making it denser and stronger. The results are essential components for high-stress applications in industries such as automotive, aerospace, and construction.
Forge presses are designed to handle immense loads, and with capacities like those offered in the GUANGDUAN Knuckle Joint Press GK Series, ranging from 6300KN to 25000KN, they can handle some of the toughest forging jobs in the industry.
The Six Core Processes of a Forge Press
How Does a Forge Press Work? To understand how a forge press works, let’s explore six crucial stages in the forging process:
1. Heating the Metal
Purpose: Heating makes the metal malleable and easier to shape.
In most forging processes, the metal workpiece is heated to high temperatures (often exceeding 1,000°C for steel). This heating softens the metal, allowing it to be deformed under pressure without breaking. The right temperature depends on the type of metal, and maintaining it consistently is crucial for quality.
2. Placing the Workpiece in the Die
Purpose: Proper alignment ensures precision in the final shape.
The die, a mold with the desired shape of the final product, is a critical component in the forging process. The metal is placed between two die halves that will compress it into shape. This step requires precise alignment since any shift can lead to deformities in the finished product.
3. Applying Pressure Using the Forge Press
Purpose: Force molds the metal into the desired shape.
Here’s where the true power of the forge press comes into play. The metal is compressed between the die halves, forcing it into every curve and corner of the die. The GUANGDUAN Knuckle Joint Press GK Series, for instance, can apply force ranging from 6300KN to 25000KN. This pressure is what shapes the metal into its final form.
4. Holding at Bottom Dead Center
Purpose: Ensures accuracy and consistency in forming.
The knuckle joint mechanism in the GK Series allows the slide to pause momentarily at the bottom dead center for about 1/18 of a cycle. This “dwell” time ensures that the metal fills every part of the die, enhancing precision. The controlled pause is essential for producing consistent results across high-stakes applications like fine stamping and extrusion.
5. Releasing the Forged Piece
Purpose: Smooth release prevents damage and prepares for inspection.
After forming, the press retracts, and the forged piece is ejected from the die. In the GUANGDUAN GK Series, the mechanical lower ejector device, a standard feature, facilitates this step. The ejection process must be gentle yet efficient to avoid damaging the freshly formed part.
6. Cooling and Finishing
Purpose: Stabilizes and prepares the piece for final use.
The forged piece is then cooled, typically at a controlled rate to maintain its structural integrity. Once cooled, it may undergo additional finishing steps, such as trimming, to remove any excess metal, and heat treatments to enhance durability and hardness.
Features and Benefits of the GUANGDUAN Knuckle Joint Press GK Series
Innovative Design for Maximum Efficiency
The GK Series from GUANGDUAN is designed with a unique knuckle joint mechanism, offering immense advantages for fine stamping and extrusion. Available in capacities from 6300KN to 25000KN, this series is versatile and adaptable. Machines with up to 16000KN capacity are built as an integral structure, while those with 12000KN use a split structure design, enhancing stability for high-force applications.
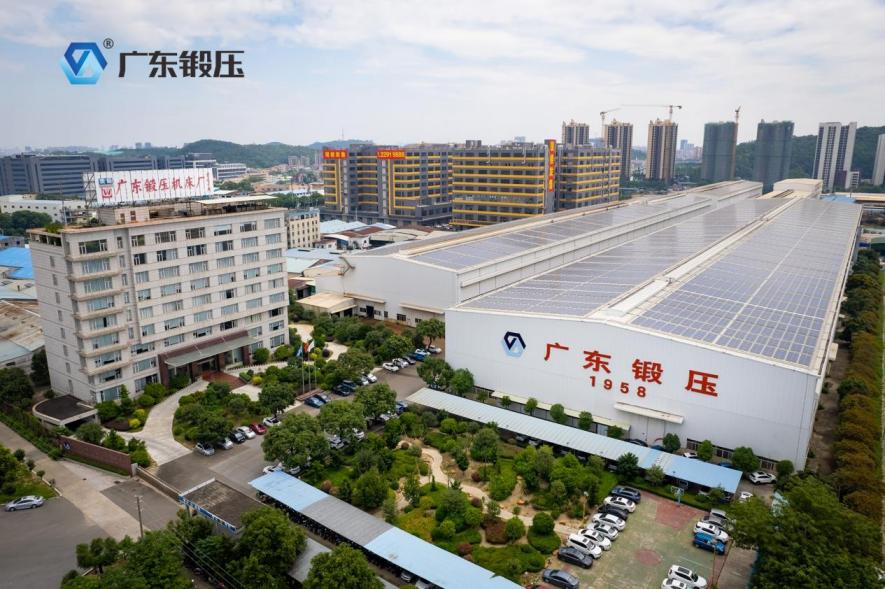
Precision and Control with Advanced Mechanisms
The GK Series is equipped with a pneumatic friction clutch brake, ensuring smooth and precise operation. Smaller models like the GK-630 use a wet integrated clutch, while larger models from GK-800 to GK-2500 employ a dry split clutch. These advanced braking mechanisms enhance control, preventing errors and making these presses ideal for delicate applications that demand high precision.
The die height indicator in the GK Series offers accuracy up to 0.01mm, a critical feature for maintaining uniformity in high-volume production. This precision allows the machine to produce consistent results, even in applications that require stringent tolerances.
PLC-Controlled Operation for Precision
The GK Series is controlled via a programmable logic controller (PLC), which adds a layer of automation and accuracy to the process. This control system allows for easy customization of operating parameters, ensuring the press meets specific production requirements and can quickly adapt to different tasks. The result? High precision, minimal waste, and the ability to handle complex stamping and extrusion tasks with ease.
Versatile Applications Across Industries
GUANGDUAN’s GK Series is widely used across various sectors, from automotive to electronics. The ability of these presses to handle fine stamping and extrusion makes them ideal for creating parts like gears, bearings, and structural components. For industries where part strength and precision are non-negotiable, a reliable forge press like the GK Series is indispensable.
Why Choose GUANGDUAN as Your Forge Press Supplier?
Founded in 1958, GUANGDUAN has more than six decades of experience in designing and manufacturing advanced metalworking machinery. As one of the top fifty backbone press machine enterprises in Guangdong province, GUANGDUAN is known for its commitment to quality, innovation, and customer satisfaction. The company operates with a team of over 800 skilled employees and employs cutting-edge technology to ensure every machine meets high standards for performance and reliability.
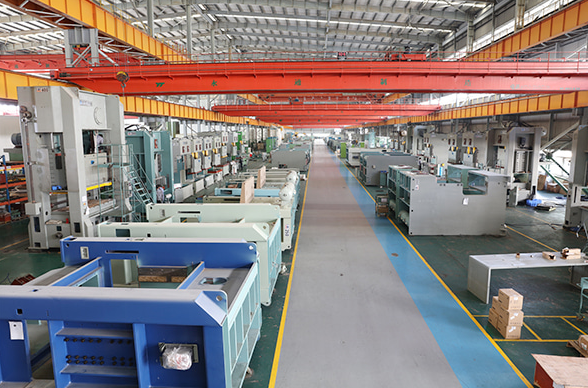
GUANGDUAN is more than a machine manufacturer; they provide comprehensive solutions for metal stamping. Whether you need a reliable press for high-stakes applications or are looking to enhance your existing operations with state-of-the-art equipment, GUANGDUAN’s expertise and dedication make them a top choice.
Conclusion: Power and Precision in Every Forge
How Does a Forge Press Work? Forge presses are the backbone of industries requiring precise and strong metal components. From heating and forming to cooling and finishing, each stage in the forging process requires exact control and powerful equipment. GUANGDUAN’s Knuckle Joint Press GK Series exemplifies this precision, offering high-force applications with accuracy down to 0.01mm.
Whether you’re exploring forging for the first time or looking to upgrade your existing equipment, understanding how a forge press works helps you appreciate the power of this technology. When it comes to finding a reliable forge press supplier, GUANGDUAN stands out with its decades of experience, commitment to quality, and innovative designs that keep industries moving forward.
CONTACT US

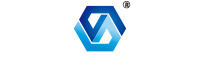
Guangdong Metal Forming Machine Works Co., Ltd.
We are always providing our customers with reliable products and considerate services.
If you would like to keep touch with us directly, please go to contact us