
Forging Press Manufacturer – Guangduan
What Does the Forging Press Mean?
Forging presses exert uniform, uniformly distributed force on a workpiece held in closed die forging by the use of a vertical ram. It’s quite similar to drop forging, although this time the pressure is applied gradually rather than rapidly. The ram’s sluggish motion allows it to reach deeper into the workpiece, resulting in more even plastic deformation.Forging Press Manufacturer.
Open and closed dies are used in press forging. When using open-die forging, the die does not surround the object being forged. The workpiece is enclosed entirely within the die during the closed die process, also known as impression die forging.
Forging presses can be hydraulic or mechanical, depending on the type of force needed. The crank mechanism drives the ram by the mechanical force generated by a flywheel that stores energy. As much as 12,000 tons of force can be applied.
Instead of using a mechanical flywheel to generate force, as is done in a traditional forging press, a hydraulic forging press uses a pressurized fluid. The force generated by large hydraulic presses can reach up to 75,000 tons.
To Make a Forge Using a Press
Forging presses come in a wide range of sizes and force capacities, all of which are used to plastically distort the workpiece. Forging requires a high level of force to be generated and concentrated on the workpiece. Using either an open or closed die, metals can be deformed and plasticized with the help of a high-performance forging press, which supplies the necessary force.
There are countless techniques that, while producing the same amount of force, are distinguished from one another by the mechanism they employ. Forging presses can be further classified based on whether or not they feature a straight or C-shaped frame. Both the C-frame and the straight-side press have one closed side.
Forging Press Designs
Forging presses come in a wide variety of designs, but the most fundamental is a mechanical press with a ram that moves vertically to apply pressure and crush a workpiece into the proper shape. In contrast to the traditional hammer and anvil technique, which bent materials by a succession of strikes, this modern forging press can achieve uniform deformation across the whole surface area of the material being worked on. Alloys with moderate ductility can be forged using a forging press, such as a hydraulic press, a single-point press, or an upsetter, all of which create the same forms.
Hydraulic Forging Presses
Forging presses that rely on hydraulic pressure from a fluid to generate force are called hydraulic presses. A ram is shaped by applying force to a fluid, which in turn pushes a greater volume of fluid to generate force. They move at a more leisurely pace than most forging presses and spend more time in touch with the material being shaped.
Hydraulic die forging typically uses open dies. Because of its moderate squeezing speed, hydraulic forging is well-suited for isothermal forging. The dies used in 50,000-ton hydraulic forging machines are 12 by 32 feet.
Because of the longer period of contact, the dies in hydraulic forging presses wear out far faster than their mechanical counterparts. The duration of contact varies with the degree of deformation necessary.
Constituents of a Hydraulic Forging Press
- The Safety Gate or Door is a disciplinary device.
- To prevent excessive motion once a specified threshold has been reached, a limit switch is installed.
- The operation can be managed with the use of a manual control valve.
- In hydraulic transfer systems, the relief valve regulates the pressure.
- The pressure gauge displays the current atmospheric pressure.
- The stroke force applied by a hydraulic cylinder only moves in one direction.
- Hydraulic fluid is kept in the high volumes oil tank.
- The pressing plate exerts a force on the workpiece.
Mechanical Forging Press
The ram of a mechanical forging press is subjected to a fixed stroke length thanks to a motor and controller outfitted with a clutch and crankshaft. At the apex of the stroke, the ram travels at its fastest, while the bottom of the stroke is where it generates the most force. Automatic forging ejection is achieved by knockout or lift-out pins.
Stress is applied to the dies with minimal impact load during the mechanical forging process. To avoid damage and breakage, tougher dies are employed. Mechanical forging presses incur substantial costs in the form of tooling and the fabrication of dies. Die costs are high, and the process of switching them out is time-consuming and labor-intensive.
As technology has advanced, mechanical forging presses have become more efficient, with several models being capable of producing 70 strokes per minute with significantly reduced human labor expenses.
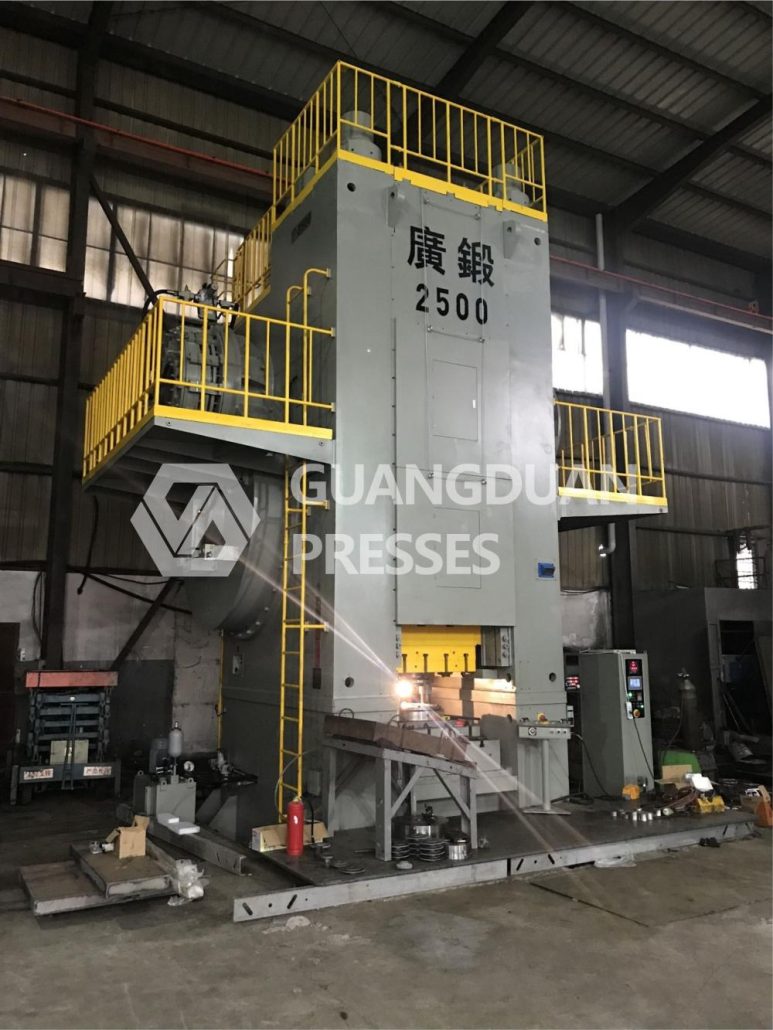
Mechanical Forging Press Components
- The forging press can’t work without the electricity provided by the engine.
- Connecting the board to the upper part of the die is the ram.
- The die consists of two halves; the top half is attached to the ram, while the bottom half rests on the base.
- The anvil is used to retain the bottom side of the die.
- In the bailing compartment, the workpiece is held while it is being molded.
Single Point Forge Press
A single-point forge press is an adjustable hydraulic press that uses one point of contact to apply force onto an object being cut. The machine applies pressure in one direction at a time, which means it can be used with any object that has a flat side or surface.
The single-point press is designed so that it can handle multiple types of materials, including cardboard, plastic sheets, and thin metal sheets. It can also be used for heavier materials such as aluminum and steel because it’s made from strong materials like stainless steel and aluminum alloys.
Servo Forging Press
The slider movement of a servo forging press is generated by a servo motor connected to an eccentric gear. By use of screws, cranking rods, and elbow rods, the linear motion of the motor’s driving force is converted into the motion of the slider. Sophisticated electronics regulate the slider’s travel distance, velocity, and force. Main drives, actuators, and auxiliary mechanisms all make up servo motor forging presses.
During the forging process, the servo motor delivers its output to the actuator, which in turn drives the slider in a reciprocating motion. Due to their modest torque, forging presses powered by servo motors are best used with relatively low tonnage.
Precision control of slider speed allows servo motor forging presses to manufacture complex components. They are cutting-edge production facilities because of their ability to conserve energy, protect the environment, serve several functions, and exhibit superior intelligence.
The production benefits of servo motor forging presses stem from the fact that the forming speed and values of each variable can be independently adjusted.
Precision Control
Tolerances of 0.0004 can be achieved with manipulation of the position siding block (0.01 mm). Precision Control Servo motor forging allows for precise control over every aspect of the forging process, leading to greater precision, longer die life, higher production, and more consistent products.
Low Noise Level
One of the most appealing features of servo motor forging presses is their relatively low noise level. For the most part, the approach significantly reduces noise levels in comparison to alternative forging methods.
Protecting the Environment
The servo motor forging technique uses less energy, has fewer moving components, and needs less oil than conventional forging methods.
Press for Forging in which the Servo Motor Does the Work
Compressed air or gas is used to power the ram of a pneumatic press, which is part of the forging process. The ram moves downhill when the cylinder is full because of the pressure created by the fluid inside. When the pressurized gas or air is released, the ram will fall.
Pneumatic Press Capable of Holding 100 Tons
An upsetter, a horizontal forging machine with a ram that moves horizontally against the workpiece, is used for upset forging or heading. A heading tool, which spreads or disturbs the end of the workpiece via metal displacement, is clamped to the workpiece and given pressure in the direction of the axis. The procedure calls for a puncher to be mounted on the header slide and two grippers and cavity dies, one of which is fixed and the other of which is coupled to the movable die slide.
The workpiece is held during the upset forging process by sliding the movable die into the stationary die. The workpiece is pressed into the die cavities as the punch or ram advances. The forging is released when the ram or punch is retracted, which leaves the movable die in an open position. It’s possible that you’ll have to do this several times before you’re done.
For upset hot forged, the workpiece is warmed to keep the metal from deforming and to improve the grain flow qualities. Stronger, more resilient metal pieces may be made thanks to the uninterrupted grain flow.
Since the height and shape of the workpiece are diminished during upset forging, this process is also known as free forming. As such, it is frequently employed in the course of a multistage forging procedure. Many ring blank fasteners forged products like bolts, screws, nuts, rivets, and flanged shafts are made via upset forging.
Now that you know all about the uses of the different forging presses you may be able to make a purchase for the one that suits your needs the best. Here at Guangduan, forging press manufacturing is specialized and we serve high-quality products.
CONTACT US

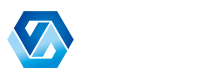
Guangdong Metal Forming Machine Works Co., Ltd.
We are always providing our customers with reliable products and considerate services.
If you would like to keep touch with us directly, please go to contact us