
Custom Forging Press Solutions: Tailoring Machines to Specific Industry Needs
Within the fiercely competitive realm of modern manufacturing, the utmost importance is placed on both precision and operational efficiency. One might find themselves contemplating how industries such as automotive and aerospace are consistently capable of producing metal components that boast exceptional quality and flawless accuracy. The underlying secret resides in the deployment of sophisticated forging press solutions, meticulously customized to satisfy the distinct demands of each specific industry. This blog ventures into the intricate landscape of bespoke forging presses, shedding light on the groundbreaking offerings from Guangduan, a preeminent supplier recognized for its excellence in this field.
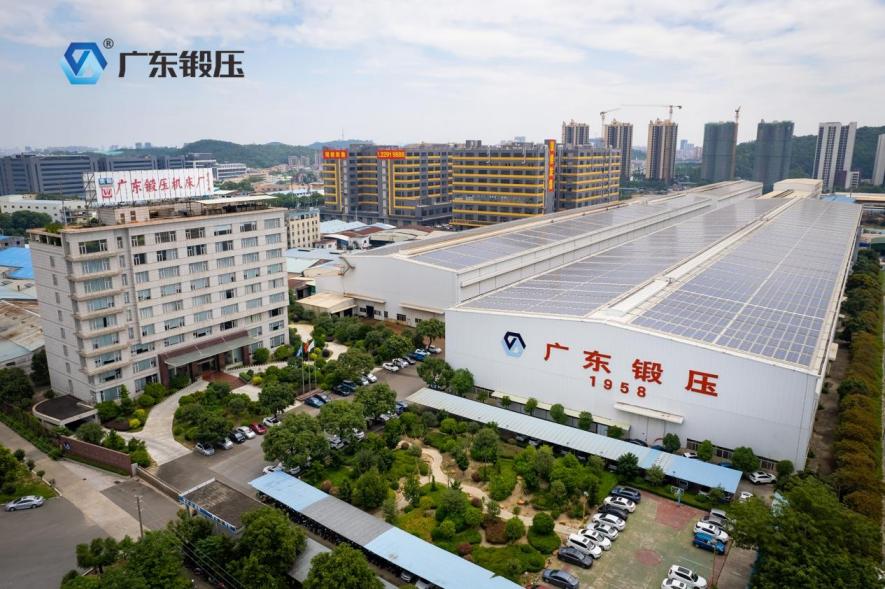
Understanding Custom Forging Press Solutions
Defining Custom Forging Press Solutions
Custom forging press solutions pertain to specialized machinery that is intricately designed to fulfill the unique requirements of diverse industries. Unlike conventional presses, these tailored machines are engineered to manage specific tasks, accommodate various materials, and handle different production volumes, thereby ensuring optimal performance and heightened efficiency. By adapting forging presses to align with the specific needs of an industry, manufacturers are empowered to achieve superior precision, minimize material waste, and significantly enhance overall productivity levels.
The Significance of Customization in Forging Presses
The act of customization holds critical importance within the forging press industry, primarily because different sectors present distinct and varied requirements. For example, the automotive industry necessitates the production of high-strength components featuring intricate designs, whereas the aerospace sector demands parts that are both lightweight and exceptionally durable. A generic, one-size-fits-all approach often proves inadequate in meeting these diverse needs effectively. Custom forging presses bridge this gap by providing flexible solutions that can be adjusted to accommodate a wide range of specifications, thereby elevating product quality and streamlining operational efficiency.
Guangduan: Pioneering Custom Forging Press Solutions
Guangduan distinguishes itself as a leading supplier of custom forging press solutions, celebrated for its innovative designs and unwavering commitment to quality. With a profound understanding of the challenges specific to various industries, Guangduan develops forging presses that are not only robust and dependable but also adaptable to the ever-evolving demands of manufacturing. Their extensive portfolio includes advanced models such as the JH31 Series Closed Type Single Point Forge Press Machine and the GK Series Knuckle Joint Press, each meticulously designed to deliver exceptional performance across a multitude of applications.
Closed Type Single Point Forge Press Machine JH31 Series
Design and Structure of the JH31 Series
The JH31 Series Closed Type Single Point Forge Press Machine epitomizes Guangduan’s engineering expertise. This narrow-table, closed-type single-point machine boasts a monolithic box-type structure, which significantly enhances its rigidity and stability. Certain models within the series are further fortified with a four-pull level pre-light structure, thereby augmenting the machine’s overall robustness. This sturdy construction ensures that the JH31 Series can effortlessly handle high-pressure forging tasks, making it ideally suited for applications that demand exceptional precision.
Key Features of the JH31 Series
A prominent feature of the JH31 Series is its eccentric shaft crankshaft, which provides remarkable bearing capacity. The incorporation of a wet-type clutch in these machines ensures an extended service life, thereby reducing the frequency of maintenance requirements. Additionally, the four-surface full-guideway slides deliver high guiding precision and outstanding holding accuracy, both of which are essential for achieving consistent and reliable forging outcomes.
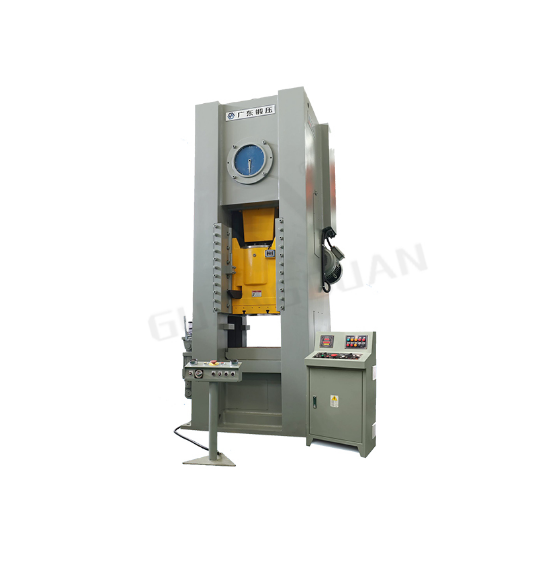
The JH31 Series is also equipped with sophisticated control mechanisms. The die set height can be adjusted mechanically and is displayed digitally, facilitating easy and rapid die calibration. Models such as the JH31-400, JH31-630, and JH31-800 are outfitted with hydraulic overload protective devices, which enhance both safety and machine longevity. In contrast, the JH31-200 and JH31-300 models feature a wedge-shaped iron die unlocking device, promoting efficient operation and ease of use.
Applications and Benefits of the JH31 Series
The versatility of the JH31 Series makes it suitable for a wide array of applications, particularly in the stamping and pressure setting processes of various metal parts. It finds extensive use in industries such as automotive, motorcycle manufacturing, daily hardware production, instrumentation, and gas appliance manufacturing. The machine’s capacity to deliver precise and consistent results renders it an invaluable asset for manufacturers striving to produce high-quality components with efficiency.
Moreover, the JH31 Series is designed to support both manual and automated production processes. Options for photo-electric protection, automatic feeding devices, and uncoiling leveling devices allow these machines to seamlessly integrate into automated production lines, thereby enhancing productivity and reducing labor costs. The compact structure and aesthetically pleasing design ensure that the machine fits harmoniously within any production environment, optimizing workspace utilization and contributing to a streamlined workflow.
Knuckle Joint Press GK Series
Design and Structure of the GK Series
The GK Series Knuckle Joint Press exemplifies Guangduan’s dedication to providing high-capacity forging solutions. These presses are available in capacities ranging from 6300KN to an impressive 25000KN, with bolster sizes varying from 700×700 mm to 1200×1200 mm. The GK Series encompasses both integral and split structure designs, thereby catering to diverse operational needs. Specifically, knuckle joint presses with capacities between 4000KN to 16000KN feature an integral structure, while those at 12000KN adopt a split structure design, offering enhanced flexibility in managing larger and more complex forging tasks.
Key Features of the GK Series
A notable attribute of the GK Series is the pneumatic wet integrated friction clutch brake found in the GK-630 series, whereas the GK-800 to GK-2500 series utilize pneumatic dry split friction clutch brakes. This variety ensures that each model within the series is capable of meeting specific performance and safety requirements tailored to different operational contexts.
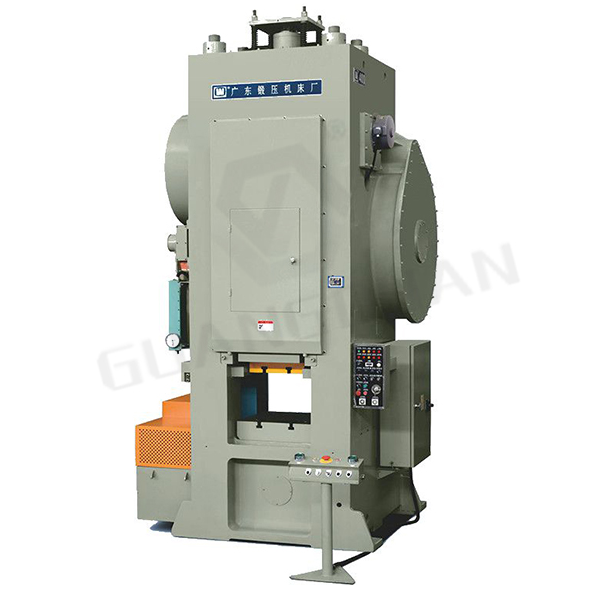
The GK Series employs a crank toggle mechanism, which allows the slide to dwell at the bottom dead center for approximately 1/18 of a cycle. This design significantly enhances the press’s efficiency and precision during the forging process. Additionally, the die height indicator provides an accurate display with a precision of 0.01mm, ensuring that operators can make meticulous adjustments to the die height as necessary.
Standard configurations of the GK Series include a mechanical lower ejector device, which facilitates the removal of forged parts and thereby streamlines the production process. Controlled by advanced PLC systems, these presses offer high precision and a sleek appearance, making them well-suited for a broad spectrum of stamping and extrusion applications.
Applications and Benefits of the GK Series
The GK Series Knuckle Joint Press is ideally suited for heavy-duty forging tasks across various industries, including automotive, aerospace, and heavy machinery manufacturing. Its high capacity and robust design make it capable of producing large and complex metal parts with remarkable precision and consistency.
One of the primary advantages of the GK Series is its versatility. Whether employed for stamping, extrusion, or other forging processes, these presses deliver reliable performance, thereby minimizing downtime and reducing maintenance costs. The advanced control systems and precise indicators further enhance operational efficiency, enabling manufacturers to achieve higher production rates without compromising on quality.
Furthermore, the aesthetic and compact design of the GK Series ensures that these presses can be effortlessly integrated into existing production lines, optimizing space and enhancing workflow. The combination of durability, precision, and flexibility positions the GK Series as a preferred choice for manufacturers seeking to elevate their forging capabilities.
Innovations and Technology in Forging Presses
Advanced Control Systems
Contemporary forging presses, such as those offered by Guangduan, incorporate state-of-the-art control systems that significantly enhance both precision and operational efficiency. The integration of PLC (Programmable Logic Controller) and pneumatic controls facilitates seamless operation and allows for real-time adjustments, ensuring that each forging cycle adheres to exact specifications. These advanced systems also simplify programming and customization, enabling manufacturers to adapt the presses effortlessly to varying production requirements.
Safety and Automation Features
Safety remains a paramount concern in forging operations, and Guangduan’s forging presses are equipped with multiple safety features designed to protect both operators and machinery. For instance, the JH31 Series includes photo-electric protection, which ensures safe machine operation by detecting any obstructions or anomalies during the forging process. Additionally, the incorporation of hydraulic overload protective devices and friction clutch brakes in the GK Series enhances machine safety and extends longevity.
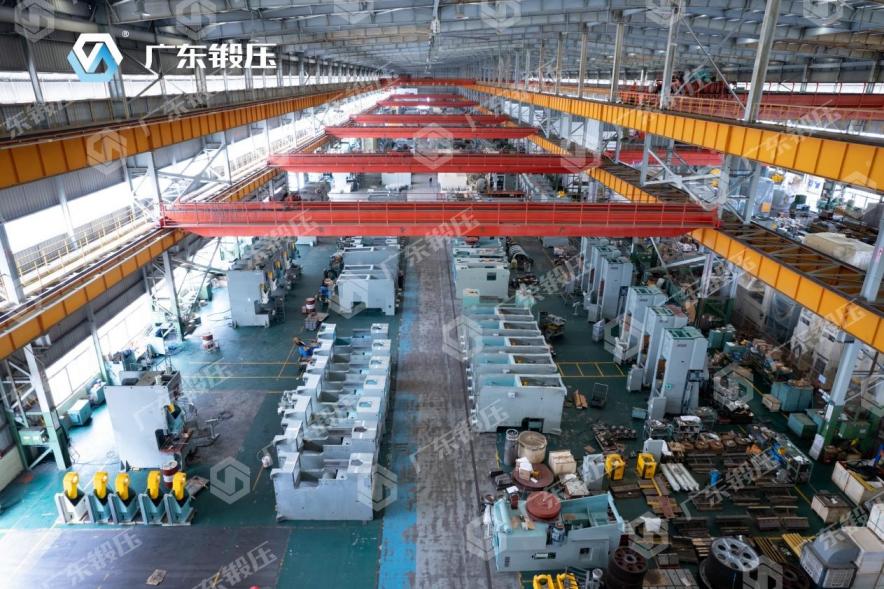
Automation features, such as automatic feeding and uncoiling leveling devices, are available with Guangduan’s presses. These automated components not only accelerate production speeds but also reduce the risk of human error, leading to more consistent and reliable forging outcomes. By integrating these advanced safety and automation technologies, Guangduan ensures that their forging presses operate with maximum efficiency while maintaining the highest safety standards.
Enhancements for Efficiency and Precision
Efficiency and precision are critical determinants of success in forging operations, and Guangduan continuously innovates to enhance these aspects. For example, the utilization of four-surface full-guideway slides in the JH31 Series provides high guiding and holding precision, ensuring that each forging cycle is both consistent and accurate. Similarly, the precise die height indicators in the GK Series allow for meticulous adjustments, thereby reducing material waste and improving overall product quality.
Moreover, the combination of mechanical and digital controls in Guangduan’s presses facilitates quick and easy calibration, minimizing downtime during production changes. These enhancements not only boost the overall efficiency of the forging process but also contribute to higher product quality, making Guangduan’s forging presses a valuable investment for manufacturers aiming to maintain a competitive edge in their respective industries.
Choosing the Right Forging Press for Your Industry
Assessing Industry-Specific Needs
Selecting the most appropriate forging press necessitates a comprehensive understanding of your industry’s specific needs. Factors such as production volume, material types, component complexity, and desired precision levels play a crucial role in determining the optimal forging press solution. For instance, the automotive industry may prioritize high-speed presses equipped with precise control systems to produce complex components, whereas the aerospace sector might require presses with higher capacity and exceptional durability to handle materials that are both lightweight and robust.

Customization Options with Guangduan
Guangduan offers an extensive array of customization options to ensure that their forging presses align perfectly with your operational requirements. Whether you require a press with a specific capacity, unique control features, or specialized safety mechanisms, Guangduan possesses the capability to tailor their machines to meet your exact specifications. This level of customization not only enhances the efficiency and effectiveness of your forging operations but also guarantees that you are equipped with machinery that can adapt to future production needs.
Furthermore, Guangduan provides comprehensive support and consultation services to assist you in selecting the right forging press. Their team of experts collaborates closely with clients to understand their unique challenges and design solutions that effectively address these issues. This collaborative approach ensures that you receive a forging press that not only meets but exceeds your expectations, propelling your business forward with reliable and high-performance machinery.
Ensuring Quality and Reliability
When making an investment in a forging press, the aspects of quality and reliability are of paramount importance. Guangduan is dedicated to delivering machines that adhere to the highest standards of quality, utilizing premium materials and advanced manufacturing techniques. Each forging press undergoes rigorous testing to verify its performance and durability, providing manufacturers with the assurance of dependable and long-lasting machinery.
CONTACT US

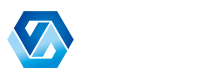
Guangdong Metal Forming Machine Works Co., Ltd.
We are always providing our customers with reliable products and considerate services.
If you would like to keep touch with us directly, please go to contact us