
Common Challenges in Forging Machine Operations and How to Overcome Them
Forging machines have transformed modern manufacturing by enabling precision, speed, and scalability. However, like all advanced machinery, forging presses face challenges during operations that can hinder productivity and lead to costly downtimes. Whether it’s ensuring the right configuration, maintaining accuracy, or avoiding wear and tear, forging machine operations come with a unique set of obstacles. How can manufacturers overcome these challenges? This blog dives deep into the common problems associated with forging machines and how innovations, such as the Knuckle Joint Press GK Series and the Closed Type Single Point Forge Press JH31 Series, are helping operators overcome them.
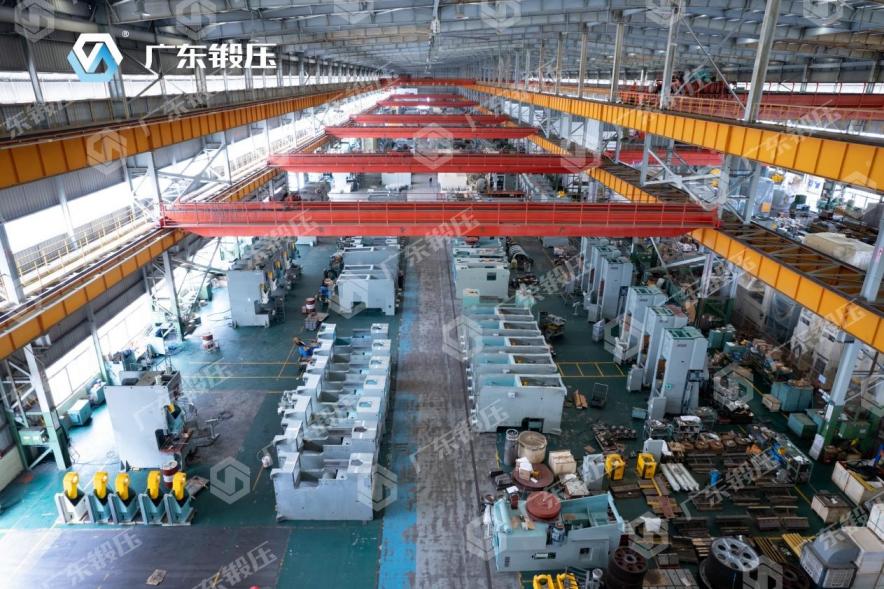
1. Challenge: Ensuring Precision in High-Pressure Forging Operations
Precision is one of the most critical aspects of forging operations, as even the smallest error in die height or positioning can compromise the entire batch of products. Forging involves extreme pressures, and maintaining accuracy at these levels can be difficult.
Precision in the Knuckle Joint Press GK Series
The Knuckle Joint Press GK Series is designed with precision in mind. One of its standout features is the die height indicator, which displays values with an accuracy of 0.01mm. This high level of accuracy is crucial in applications like fine stamping and extrusion processes, where even the smallest deviations in measurement can result in poor-quality products. The GK Series presses use a crank toggle mechanism that allows the slide to dwell at the bottom dead center for around 1/18 cycle, adding an additional layer of control.
JH31 Series: Precision with Versatility
Similarly, the JH31 Series Closed Type Single Point Forge Press addresses the challenge of maintaining precision through its digital die height display and mechanical adjustment capabilities. The ease of calibration means that operators can make swift, accurate adjustments without extensive downtime. This ensures that the forging press consistently meets the desired specifications, regardless of the application.
Overcoming the Challenge with PLC Control
Both the GK Series and JH31 Series incorporate PLC (Programmable Logic Controller) systems. The role of the PLC in maintaining precision is indispensable, as it enables automated control, reducing the chance for human error and ensuring consistency across production cycles. By integrating digital controls, these machines offer enhanced precision, even under high-stress conditions.
2. Challenge: Managing Wear and Tear
Forging machines, especially those operating in high-volume industries, experience significant wear and tear over time. Components like the clutch, bearings, and slides are subjected to immense pressure, heat, and friction, which can lead to frequent breakdowns if not adequately addressed.
Durability in the GK Series
The Knuckle Joint Press GK Series addresses this challenge with advanced materials and design. For instance, the machines feature a pneumatic wet integrated friction clutch brake (GK-630 series) and a pneumatic dry split friction clutch brake (GK-800 to GK-2500). These features not only provide superior stopping power but also reduce the heat generated during operations, thereby minimizing wear on the clutch. Moreover, the GK-12000 adopts a split-structure design, which adds to its durability by distributing the mechanical stress across the machine’s frame more effectively.
Long Service Life in the JH31 Series
The JH31 Series features a wet-type clutch known for its extended service life. In high-pressure environments, this is crucial as it ensures that the machine can run continuously with fewer interruptions for maintenance. The design of the JH31 also includes a four-surface full-guideway slide block, which improves the guiding precision while reducing unnecessary friction, further enhancing the longevity of the machine.
Routine Maintenance and Material Innovations
Regular maintenance is a key strategy to manage wear and tear. Both the GK Series and JH31 Series are designed for easy maintenance with clear indicators for wear. Innovations in materials, such as hardened steel for critical components, ensure that these machines can withstand the intense pressures of forging, reducing the need for frequent replacements and repairs.
3. Challenge: Enhancing Safety in Forging Operations
Forging processes involve extreme forces and temperatures, making safety a major concern for operators. Without proper safety mechanisms, accidents are not only possible but likely, given the nature of the work. Protecting workers while maintaining productivity is a constant challenge in forging machine operations.
Safety Features in the Knuckle Joint Press GK Series
The GK Series integrates several key safety features. For instance, it comes with a mechanical lower ejector device as part of its standard configuration. This device ensures that the workpiece is ejected without requiring manual handling, reducing the risk of injury. Additionally, the PLC-controlled system provides more accurate monitoring and control, allowing operators to manage the machine safely and efficiently.
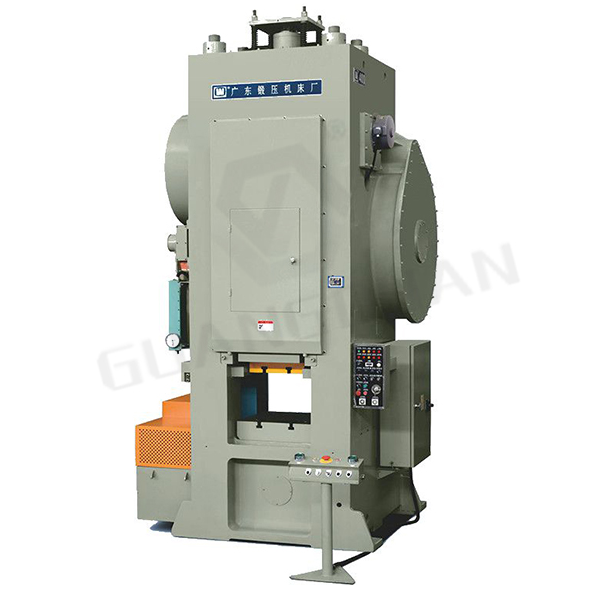
Safety and Automation in the JH31 Series
The JH31 Series takes safety to another level by offering optional photo-electric protection. This system uses sensors to detect any abnormalities in the forging area, automatically stopping the machine if there’s a safety risk. Moreover, the JH31 can be fitted with an automatic feeding device and an uncoiling leveling device, enabling automated production. This minimizes human intervention in hazardous areas, further improving operator safety.
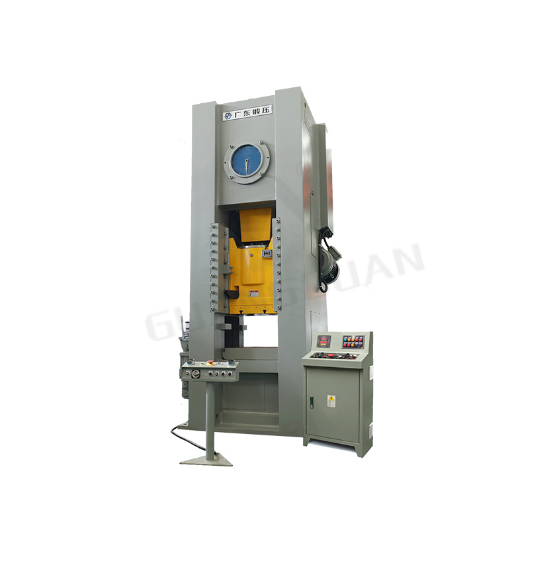
Hydraulic Overload Protection
One of the standout safety features in the JH31 Series is its hydraulic overload protective device, which is standard on the JH31-400/630/800 models. This feature is crucial for preventing catastrophic failures that could result from mechanical overloads, thus safeguarding both the machine and its operators. By automatically shutting down the machine when it detects an overload, the system ensures that accidents are avoided, and the equipment remains intact.
4. Challenge: Maximizing Efficiency in High-Volume Production
In industries like automotive, daily hardware, and gas appliances, forging operations need to be both high-precision and high-speed. Meeting large-scale production demands while maintaining quality can be an overwhelming challenge for operators.
High-Volume Capabilities in the GK Series
The Knuckle Joint Press GK Series offers capacity ranging from 6300KN to 25000KN, making it suitable for various high-volume forging applications. Its mechanism, designed to allow the slide to dwell at the bottom dead center, provides operators with greater control, leading to more consistent and precise results, even in large batches. The integral structure design, which applies to presses from 4000KN to 16000KN, enhances stability during high-volume operations, reducing the risk of errors or malfunctions.
Automation in the JH31 Series for Greater Throughput
The JH31 Series addresses the need for speed and volume with its automation features. By incorporating automatic feeding and uncoiling leveling devices, this forge press is designed to operate continuously without constant human intervention. This drastically reduces cycle times, allowing manufacturers to achieve higher throughput. The combination of PLC and pneumatic control also ensures that the machine operates efficiently, whether in continuous, single-stroke, or micro-motion modes.
Combining Precision and Speed
Both the GK Series and JH31 Series exemplify how modern forging machines can blend precision with speed. The ability to adjust the die height quickly and accurately, along with integrated safety and automation features, ensures that these machines can handle the demands of large-scale production without sacrificing quality.
Conclusion: Overcoming Forging Challenges with Advanced Machines
The challenges faced by forging machine operators—precision, wear and tear, safety, and efficiency—are significant but not insurmountable. Advanced machines like the Knuckle Joint Press GK Series and the Closed Type Single Point Forge Press JH31 Series from GUANGDUAN are equipped with innovative solutions that tackle these problems head-on. With features like PLC control, durable components, and automated safety systems, these machines ensure that manufacturers can maintain high productivity while minimizing risks and costs. As the forging industry continues to evolve, machines like these will play a pivotal role in shaping its future.
CONTACT US

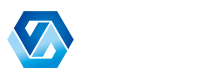
Guangdong Metal Forming Machine Works Co., Ltd.
We are always providing our customers with reliable products and considerate services.
If you would like to keep touch with us directly, please go to contact us