
Precision Aerospace Aluminum Alloy Stamping: Knuckle Joint Press Technology
The demand for high precision in aerospace manufacturing is increasing. Many industries need accurate and strong metal parts. One important technology for this is the knuckle joint press. It plays a key role in shaping aluminum alloy through stamping.
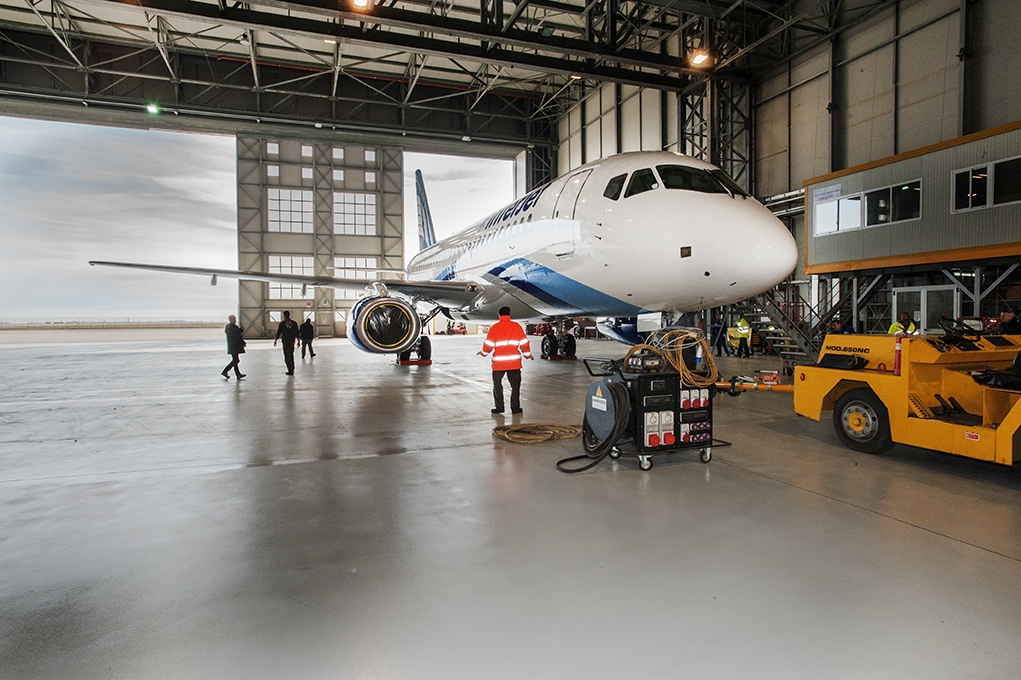
The GK series is a type of forging press. It offers a capacity from 6300KN to 25000KN. The bolster size ranges from 700×700 mm to 1200×1200 mm. Knuckle joint presses with capacities from 4000KN to 16000KN use an integral structure. Let’s dive in!
What is Knuckle Joint Press Technology?
Explanation of Knuckle Joint Press Mechanics and Functionality
A knuckle joint press is a type of forging machine. It is used to shape metal parts with high precision. This press works by using a special linkage system. The system moves the press slide with strong force and slow speed. This allows the machine to apply pressure in a controlled way.
The main part of the press is the knuckle joint mechanism. It connects the driving shaft to the slide. When the machine moves, the knuckle joint transfers force smoothly. This design makes the machine press metal with even pressure. It is useful for shaping strong materials like aluminum alloys.
How It Differs from Other Stamping Technologies
The knuckle joint press is different from other stamping machines. A regular stamping press moves the slide up and down in a straight line. It applies force quickly. But a knuckle joint press moves the slide more slowly at the bottom. This slow movement helps to form parts with better precision.
Another difference is the force distribution. In a regular press, the force is highest in the middle of the stroke. In a knuckle joint press, the force is strongest at the bottom. This helps to press metal more evenly. It reduces the risk of defects in the final product.
Advantages for High-Precision Aerospace Components
Aerospace components need to be very accurate. Even small errors can affect performance. The knuckle joint press helps make parts with high precision. Since it moves slowly at the bottom, it allows better control. This makes it perfect for forming complex aerospace parts.
The press also reduces stress on the metal. This prevents cracks and weak points in the parts. In aerospace manufacturing, strong and lightweight materials are important. The knuckle joint press ensures that stamped parts meet strict quality standards.
Importance of Aerospace Aluminum Alloy Stamping
Characteristics of Aerospace-Grade Aluminum Alloys
Aluminum alloys used in aerospace are different from regular aluminum. They are made with special elements to make them stronger. These alloys have high strength but remain lightweight. This balance is important for aircraft performance.
Another key feature is corrosion resistance. Airplanes operate in extreme conditions. They face moisture, heat, and pressure changes. Aerospace aluminum alloys do not rust easily. This helps them last longer.
Why Precise Stamping is Critical for Structural Integrity and Performance
Precision is very important in aerospace manufacturing. Parts need to fit perfectly. If a stamped aluminum part is not accurate, it can cause problems in the aircraft. Small errors can lead to weak spots. This can affect safety.
Stamped parts must also be strong. If a part has defects, it might break under pressure. The knuckle joint press ensures each part is shaped correctly. It reduces material stress and keeps the metal structure strong.
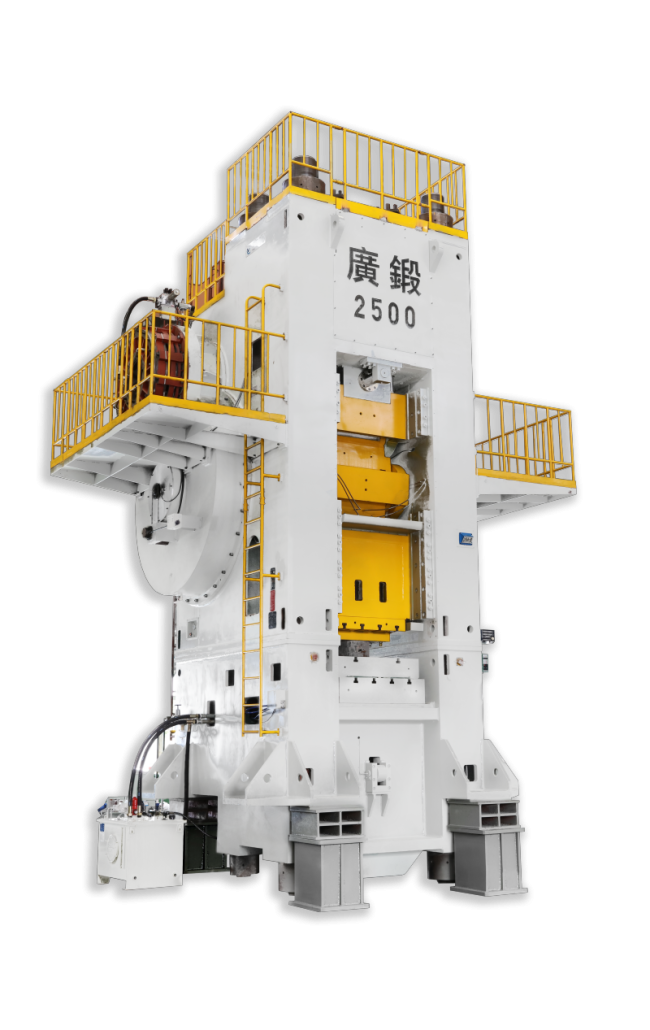
Common Uses of Stamped Aluminum Alloy Parts in Aerospace
Stamped aluminum parts are used in many aerospace applications. One common use is aircraft body panels. These panels need to be both strong and lightweight. Stamping allows manufacturers to create thin yet durable panels.
Another use is in engine components. Aircraft engines face high temperatures and pressure. Stamped aluminum parts help in cooling systems, fuel systems, and air ducts. They need to be precise to work properly.
Other parts include landing gear components and interior structural parts. Stamping helps create uniform and high-quality parts for all these applications.
How Knuckle Joint Press Enhances Precision
Pneumatic Wet and Dry Friction Clutch Brake Systems
Different knuckle joint press models use different clutch systems. The GK-630 series uses a pneumatic wet integrated friction clutch brake. This system reduces wear and increases efficiency.
Models from GK-800 to GK-2500 use a pneumatic dry split friction clutch brake. This system provides faster response and better control. It allows the machine to apply pressure with great accuracy.
Crank Toggle Mechanism for Smooth Operation
The knuckle joint press uses a crank toggle mechanism. This system controls the movement of the slide. It allows the slide to stop for a short moment at the bottom. This moment is around 1/18 of a full cycle.
This pause at the bottom helps in high-precision forming. The pressure is applied evenly, which reduces defects. It also makes sure that each stamped part has the exact shape needed.
High-Precision Die Height Indicator
Precision is important in aerospace manufacturing. The die height indicator on the knuckle joint press helps with accuracy. It shows a display value of 0.01mm. This level of precision ensures that stamped parts are consistent.
The machine also includes a mechanical lower ejector device. This feature helps remove stamped parts smoothly. It prevents damage to the parts after stamping.
PLC-Controlled System for Accuracy and Efficiency
The knuckle joint press is controlled by a PLC (Programmable Logic Controller). This system makes sure the machine runs accurately. It controls the movement, pressure, and speed of the press.
A PLC-controlled system also makes the machine easy to operate. It allows manufacturers to set the exact stamping parameters. This ensures repeatable results and high-quality parts.
Advantages for Aerospace Manufacturers
Improved Productivity and Reduced Waste
Aerospace manufacturing needs to be efficient. The knuckle joint press helps increase productivity. It allows fast and precise stamping of parts. Since the machine applies force evenly, it reduces material waste.
Less waste means lower costs. It also helps in making production more sustainable. Manufacturers can use materials more efficiently and reduce scrap.
Enhanced Part Durability and Reduced Risk of Defects
Durability is important for aerospace parts. A small defect can cause failure. The knuckle joint press ensures that each part is shaped correctly. The slow movement at the bottom helps in forming strong and reliable parts.
Defects like cracks or uneven surfaces are reduced. This makes the parts safer and longer-lasting. Aerospace manufacturers can trust the quality of stamped parts.
Lower Production Costs Through More Efficient Processes
Efficiency in manufacturing helps reduce costs. The knuckle joint press offers a more controlled stamping process. This reduces errors and rework. It also reduces the need for additional machining.
Since stamped parts require less finishing work, manufacturers save time and money. This makes the production process smoother. It also helps meet high industry standards without extra costs.
Upgrade Your Aerospace Manufacturing with Knuckle Joint Press
Knuckle joint presses improve precision. They shape aluminum alloys with strong and even force. They reduce material stress. They help create accurate aerospace parts. They also lower defects and waste.
The GK series offers reliable performance. It uses advanced clutch systems. It ensures high accuracy with a precise die height indicator. It is PLC-controlled for better efficiency.
Improve your production. Reduce costs. Enhance part durability. Choose a knuckle joint press for better results. Contact us today to learn more!
CONTACT US

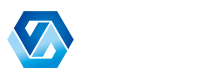
Guangdong Metal Forming Machine Works Co., Ltd.
We are always providing our customers with reliable products and considerate services.
If you would like to keep touch with us directly, please go to contact us