
Investing in Advanced Forge Hydraulic Press: Future-Proofing Your Business
In today’s rapidly evolving industrial landscape, businesses face the constant challenge of staying ahead of technological advancements to maintain competitiveness. Is your manufacturing process equipped to handle the demands of the future? Investing in advanced forge hydraulic presses can be the key to future-proofing your operations, ensuring efficiency, precision, and scalability.
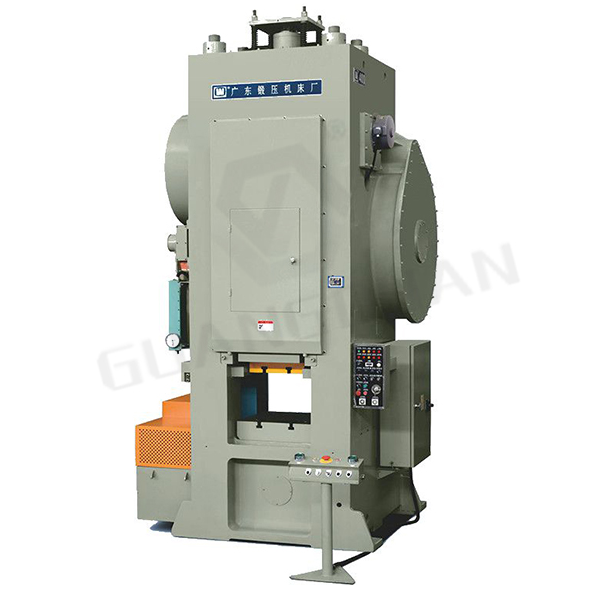
Enhancing Operational Efficiency
Advanced forge hydraulic presses, such as the Knuckle Joint Press GK Series from GUANGDUAN, are designed to optimize production processes. These presses offer a wide range of capacities, from 6,300KN to 25,000KN, catering to diverse manufacturing needs. By integrating these powerful machines into your production line, businesses can achieve higher throughput rates without compromising on quality.
Moreover, the robust design of the GK Series ensures minimal downtime and maintenance requirements. The pneumatic wet integrated friction clutch brake in the GK-630 series and the pneumatic dry split friction clutch brake in the GK-800 to GK-2500 series provide reliable stopping power, enhancing overall machine longevity. This reliability translates to consistent production schedules and reduced operational disruptions.
Additionally, the crank toggle mechanism allows the slide to dwell at the bottom dead center for approximately 1/18 of a cycle, facilitating precise control over the forging process. This feature not only improves product accuracy but also enhances energy efficiency, contributing to lower operational costs and a more sustainable manufacturing process.
Scalability and Flexibility
As businesses grow, their manufacturing needs evolve. The GK Series knuckle joint presses offer scalability with their varying capacities and bolster sizes, ranging from 700700mm to 1,2001,200mm. This flexibility allows manufacturers to scale their operations seamlessly, accommodating larger production volumes or more complex forging tasks as demand increases.
The split structure design in the 12,000KN model further enhances flexibility, enabling easier customization and adaptation to specific production requirements. This adaptability ensures that businesses can respond swiftly to market changes and customer demands, maintaining a competitive edge in the global market.
Furthermore, the integration of programmable logic controllers (PLCs) in the GK Series ensures that each press can be fine-tuned to meet specific production parameters. This level of control allows manufacturers to produce a wide variety of components with high precision, catering to multiple industries and applications.
Long-Term Investment Benefits
Investing in advanced forge hydraulic presses is not merely a short-term solution but a strategic decision for long-term growth. The GK Series presses from GUANGDUAN are built with cutting-edge technology and superior materials, ensuring durability and longevity. This durability reduces the need for frequent replacements, lowering long-term capital expenditures.
Additionally, the precision and reliability of these presses contribute to higher-quality products, which can enhance a company’s reputation and market position. Superior product quality often leads to increased customer satisfaction and loyalty, driving repeat business and expanding market share.
Moreover, the energy-efficient features of the GK Series, such as the pneumatic clutch brakes and efficient motor designs, contribute to lower energy consumption. This not only reduces operational costs but also aligns with global sustainability trends, positioning businesses as environmentally responsible leaders in their industries.
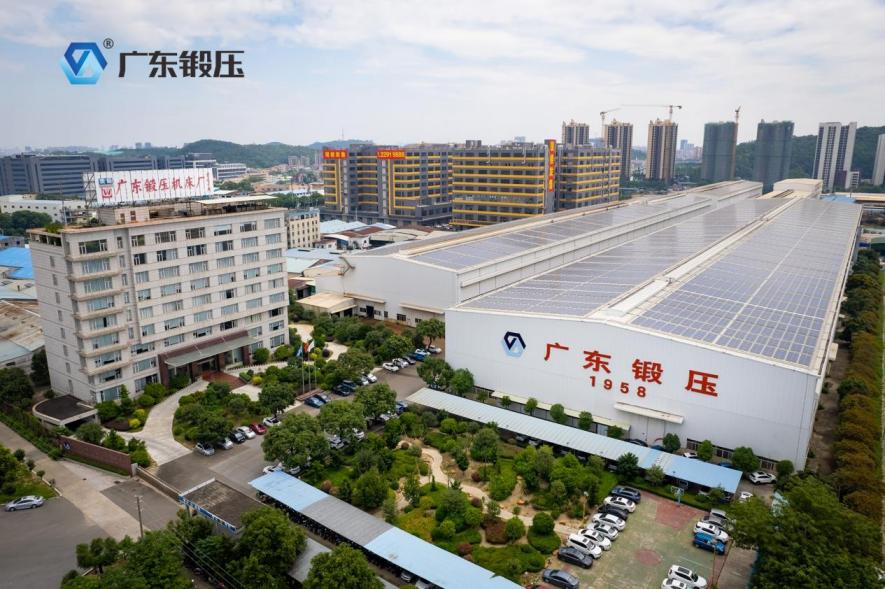
The Role of Automation in Modern Forge Hydraulic Press Manufacturing
Automation has revolutionized manufacturing, and the forge hydraulic press industry is no exception. How is automation transforming the production of forge hydraulic presses, and what benefits does it bring to manufacturers? The integration of automation technologies in forge hydraulic press manufacturing is enhancing precision, efficiency, and overall production quality.
Precision and Consistency
Automation plays a crucial role in ensuring precision and consistency in forge hydraulic press manufacturing. The GK Series knuckle joint presses are controlled by PLCs, which allow for meticulous adjustments and real-time monitoring of production parameters. This level of control ensures that each press is manufactured to exact specifications, reducing the margin of error and enhancing product quality.
Automated systems also facilitate the precise alignment and assembly of components, minimizing human error and ensuring that every press operates smoothly and efficiently. This precision is particularly important in high-capacity presses, where even minor discrepancies can lead to significant performance issues.
Furthermore, automation enables consistent repeatability in the manufacturing process. By standardizing production steps, automated systems ensure that each forge hydraulic press meets the same high standards, providing customers with reliable and dependable machinery.
Increased Production Efficiency
The incorporation of automation in forge hydraulic press manufacturing significantly boosts production efficiency. Automated assembly lines streamline the production process, reducing the time required to manufacture each press. This increased efficiency allows manufacturers to meet higher demand without compromising on quality or increasing production costs.
Additionally, automation facilitates faster changeovers between different press models. The GK Series offers a variety of configurations, and automated systems enable quick adjustments to accommodate different specifications. This flexibility ensures that manufacturers can respond swiftly to market demands and customize presses to meet specific customer requirements.
Moreover, automated quality control systems continuously monitor the manufacturing process, identifying and addressing potential issues in real-time. This proactive approach minimizes waste, reduces rework, and ensures that each press adheres to stringent quality standards, ultimately enhancing overall production efficiency.
Enhanced Safety and Reduced Labor Costs
Automation in forge hydraulic press manufacturing also enhances workplace safety. Automated systems handle repetitive and hazardous tasks, reducing the risk of workplace accidents and injuries. This not only protects employees but also minimizes downtime and associated costs related to workplace incidents.
Furthermore, automation reduces the reliance on manual labor, lowering labor costs and increasing overall productivity. By automating routine tasks, manufacturers can reallocate their workforce to more skilled and value-added activities, fostering innovation and continuous improvement within the organization.
The integration of advanced automation technologies in the GK Series presses also simplifies the manufacturing process, making it easier to train employees and maintain consistent production standards. This streamlined approach contributes to a more efficient and cost-effective manufacturing operation.
Challenges and Opportunities in the Global Forge Hydraulic Press Market
The global forge hydraulic press market is dynamic, presenting both challenges and opportunities for manufacturers. What are the key factors influencing this market, and how can businesses navigate them to achieve success? Understanding the complexities of the global market is essential for leveraging opportunities and overcoming obstacles in the forge hydraulic press industry.
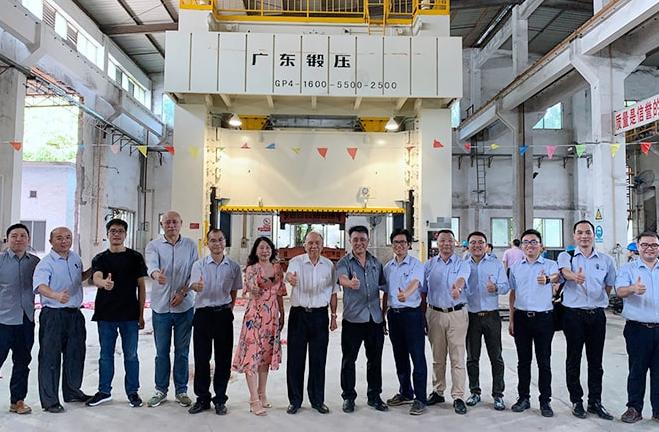
Market Competition and Innovation
One of the primary challenges in the global forge hydraulic press market is intense competition. Numerous manufacturers are vying for market share, making it essential to differentiate products through innovation and quality. The GK Series knuckle joint presses from GUANGDUAN exemplify this approach, offering advanced features such as pneumatic friction clutch brakes and precise die height indicators to stand out in a crowded market.
Continuous innovation is crucial for maintaining a competitive edge. Manufacturers must invest in research and development to incorporate the latest technologies and improve press performance. Features like PLC control systems, automated quality checks, and energy-efficient designs are increasingly becoming standard expectations in the market.
Additionally, offering customized solutions can help businesses cater to specific customer needs and establish strong relationships. The flexibility of the GK Series, with its range of capacities and bolster sizes, allows manufacturers to tailor presses to diverse applications, enhancing their appeal to a broader customer base.
Supply Chain and Global Logistics
Navigating the complexities of global supply chains poses another significant challenge. Fluctuations in raw material prices, transportation delays, and geopolitical tensions can impact the availability and cost of components required for forge hydraulic press manufacturing. Ensuring a resilient and flexible supply chain is vital for maintaining production schedules and meeting customer demands.
Partnering with reliable suppliers and diversifying the supply base can mitigate risks associated with supply chain disruptions. GUANGDUAN’s strategic sourcing of high-quality materials and components ensures that the GK Series presses maintain their superior performance and reliability, even in the face of supply chain challenges.
Moreover, leveraging advanced supply chain management technologies can enhance visibility and efficiency. Implementing real-time tracking systems and predictive analytics allows manufacturers to anticipate and address potential disruptions proactively, ensuring smooth and uninterrupted production processes.
Emerging Markets and Growth Opportunities
Despite the challenges, the global forge hydraulic press market presents numerous growth opportunities, particularly in emerging markets. Rapid industrialization and infrastructure development in regions such as Asia-Pacific, Africa, and Latin America are driving demand for high-capacity forging machinery. The GK Series, with its extensive range of capacities and robust features, is well-positioned to capitalize on this growing demand.
Investing in emerging markets requires a deep understanding of local market dynamics and customer preferences. Establishing strong distribution networks and providing localized support can enhance market penetration and customer satisfaction. GUANGDUAN’s global presence and commitment to customer-centric solutions enable the company to effectively serve diverse markets and tap into new growth opportunities.
Furthermore, the increasing emphasis on sustainable manufacturing practices presents an opportunity for manufacturers to differentiate themselves. By offering eco-friendly forge hydraulic presses with energy-efficient features and reduced emissions, businesses can attract environmentally conscious customers and comply with stringent environmental regulations.
Case Studies: Successful Implementations of Forge Hydraulic Presses Across Different Industries
Real-world applications of forge hydraulic presses demonstrate their versatility and impact across various industries. How have businesses leveraged advanced hydraulic presses to enhance their operations and achieve remarkable results? Exploring these case studies provides valuable insights into the practical benefits and transformative potential of forge hydraulic presses like the GK Series.

Automotive Industry: Enhancing Component Precision
In the automotive sector, precision and reliability are paramount. A leading automotive parts manufacturer integrated the GK-1200 knuckle joint press into their production line to improve the forging process of critical components such as engine parts and chassis components. The press’s 12,000KN capacity and precise die height indicator ensured consistent quality and accuracy, reducing defects and enhancing product performance.
The automation features of the GK-1200, including PLC control and mechanical lower ejector devices, streamlined the production process, increasing throughput while maintaining stringent quality standards. This implementation led to a significant reduction in production costs and turnaround times, enabling the manufacturer to meet the high demands of the automotive market efficiently.
Furthermore, the robust design and reliability of the GK-1200 minimized downtime, ensuring uninterrupted production schedules and enhancing overall operational efficiency. This case highlights how advanced forge hydraulic presses can drive improvements in precision, efficiency, and cost-effectiveness within the automotive industry.
Aerospace Industry: Achieving High-Strength Components
The aerospace industry demands materials and components that exhibit exceptional strength and durability. A prominent aerospace manufacturer adopted the GK-2500 knuckle joint press to forge high-strength components used in aircraft structures. The press’s impressive 25,000KN capacity and large bolster size of 1,500*1,200mm allowed for the production of sizable and complex components with high precision.
The integration of automated controls and advanced braking systems in the GK-2500 ensured meticulous control over the forging process, resulting in components that met the stringent safety and performance standards of the aerospace industry. The mechanical lower ejector device facilitated the efficient removal of forged parts, enhancing production speed and reducing cycle times.
This successful implementation demonstrated the GK-2500’s capability to meet the demanding requirements of the aerospace sector, showcasing its role in producing high-strength, reliable components essential for aircraft performance and safety.
Heavy Machinery Industry: Boosting Production Capacity
In the heavy machinery industry, the ability to produce large and robust components is crucial. A leading manufacturer of construction equipment integrated the GK-8000 knuckle joint press into their production line to forge heavy-duty parts such as hydraulic cylinders and frame components. The press’s 8,000KN capacity and substantial bolster size of 900*1,000mm provided the necessary power and stability to handle large-scale forging tasks.
The pneumatic dry split friction clutch brake system of the GK-8000 ensured smooth and precise operation, enhancing the quality of the forged parts. The crank toggle mechanism allowed for efficient control over the forging cycle, optimizing production speed and reducing energy consumption.
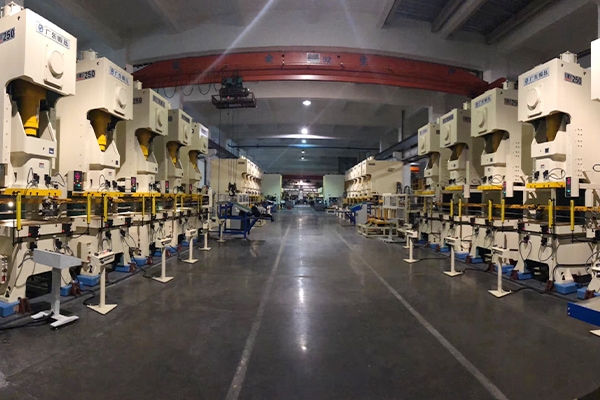
As a result, the manufacturer experienced a significant increase in production capacity and efficiency, enabling them to meet the growing demand for heavy machinery components. The successful implementation of the GK-8000 underscored the press’s effectiveness in boosting production capabilities and supporting the high-output needs of the heavy machinery industry.
Conclusion
The global forge hydraulic press market is poised for continued growth, driven by advancements in technology, increasing demand across various industries, and the need for efficient and reliable manufacturing solutions. Investing in advanced forge hydraulic presses, such as the Knuckle Joint Press GK Series from GUANGDUAN, offers businesses the opportunity to future-proof their operations, enhance production efficiency, and maintain a competitive edge in the global market.
Automation plays a pivotal role in modern forge hydraulic press manufacturing, enabling precision, consistency, and increased production efficiency while enhancing workplace safety and reducing labor costs. Navigating the challenges of market competition and global supply chains requires innovation, strategic partnerships, and a commitment to quality and customization.
Successful implementations across industries like automotive, aerospace, and heavy machinery demonstrate the transformative impact of advanced forge hydraulic presses. These case studies highlight the versatility and effectiveness of the GK Series in meeting diverse manufacturing needs, driving operational improvements, and achieving remarkable results.
As the global market continues to evolve, businesses that invest in advanced forge hydraulic press technologies and leverage automation will be well-positioned to capitalize on emerging opportunities and overcome challenges. By partnering with reputable suppliers like GUANGDUAN, manufacturers can ensure they have access to cutting-edge equipment and support, enabling them to thrive in an increasingly competitive and dynamic industrial landscape.
About GUANGDUAN
GUANGDUAN is a leading supplier of high-quality forge hydraulic presses, including the renowned Knuckle Joint Press GK Series. With a commitment to innovation, precision, and customer satisfaction, GUANGDUAN provides advanced forging solutions tailored to meet the diverse needs of global industries. Explore the GK Series and discover how GUANGDUAN can help elevate your manufacturing operations to new heights.
Tags
#forgehydraulicpress #GKSeries #manufacturing #automation #globalmarket #GUANGDUAN #industrialmachinery #forging #innovation #precisionengineering #sustainability #automationinmanufacturing #casestudies #industrialautomation #futureproofing #heavyindustries #automotive #aerospace #heavymachinery #manufacturingtechnology
CONTACT US

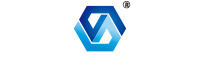
Guangdong Metal Forming Machine Works Co., Ltd.
We are always providing our customers with reliable products and considerate services.
If you would like to keep touch with us directly, please go to contact us