
Advanced Stamping Machine for Modern Manufacturing
Have you ever found yourself considering how the intricate and precise metal components, which are commonly found in vehicles, household devices, or even in electronic gadgets, are manufactured with such astonishing accuracy? It might come as a surprise to learn that, behind the operations of many industries, an extremely powerful and adaptable machine works tirelessly, shaping raw metals into vital components that play a significant role in our technologically advanced world. This machine, known as the stamping press, has risen to an indispensable position in the manufacturing sector, particularly as the demand for mass-produced, high-quality metal parts escalates continuously. As these industries rely more and more heavily on such technology, stamping machines have transformed into even more advanced, flexible, and efficient tools than ever before.
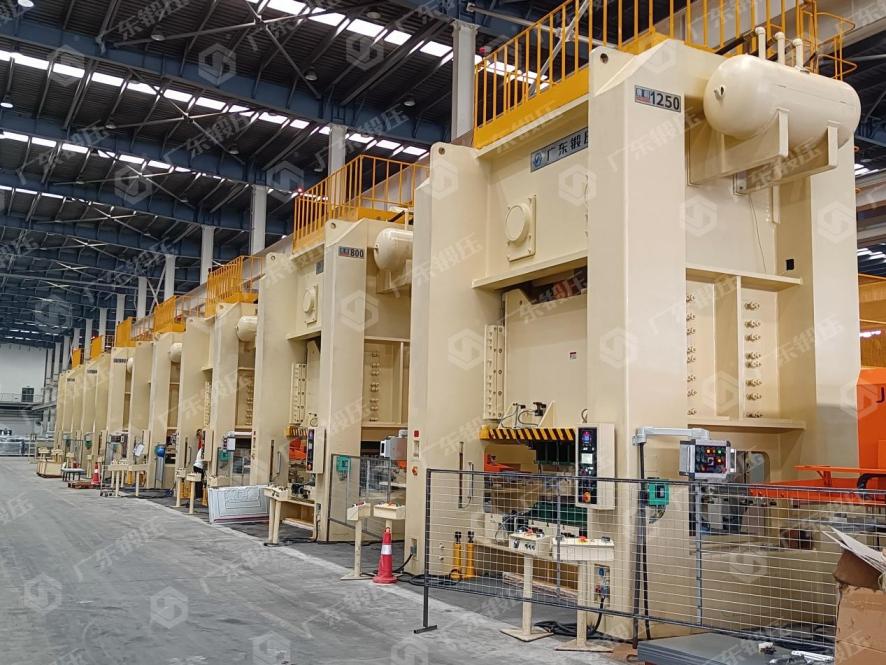
An Expanding Demand for Stamping Machine Across Diverse Sectors
In today’s swiftly accelerating industrial landscape, the growing expectations for precision, operational efficiency, and the scalability of production processes confront companies with mounting challenges. As sectors such as automotive, aerospace, consumer electronics, and household goods experience exponential growth, the need for precise and efficient stamping machine has also risen at an unprecedented rate. Whether the task demands cutting, forming, or assembling metal parts, stamping machine provides an unparalleled solution that guarantees consistent, high-quality production at scale.
Automotive Industry
The reliance of the automotive industry on stamping machine is unmistakable, particularly when it concerns the manufacturing of critical metal parts, ranging from the body panels that define the structure of a vehicle to the intricately engineered engine components that drive performance. With a continuous increase in consumer demand for vehicles, coupled with the technological revolution ushered in by electric cars, the necessity for precision within the stamping process has reached an unprecedented level. Specifically, high-speed presses have become essential, as they make it possible to rapidly manufacture components while maintaining rigorous standards of consistency and accuracy, even when used for mass production.
Electronics and Technology
As the world becomes increasingly interconnected and technology permeates every aspect of modern life, the demand for highly efficient and precise electronic devices has skyrocketed. Stamping machine is integral to the creation of key components for such devices, including metal frames, connectors, and other small parts vital to smartphones, computers, and various electronic gadgets. As these devices continue to shrink in size and grow in sophistication, stamping machine is tasked with the challenge of producing smaller, more complex parts at faster speeds, all without compromising the quality or precision of the final product.
Hydraulic Stamping Machine GY2S Series: A Benchmark of Precision and Versatility
Among the numerous stamping machines available today, the Hydraulic Press GY2S Series distinguishes itself by its extraordinary performance and unmatched precision. This press has been specifically designed to offer manufacturers a harmonious blend of flexibility, durability, and efficiency, making it an attractive option for a wide variety of industrial applications.
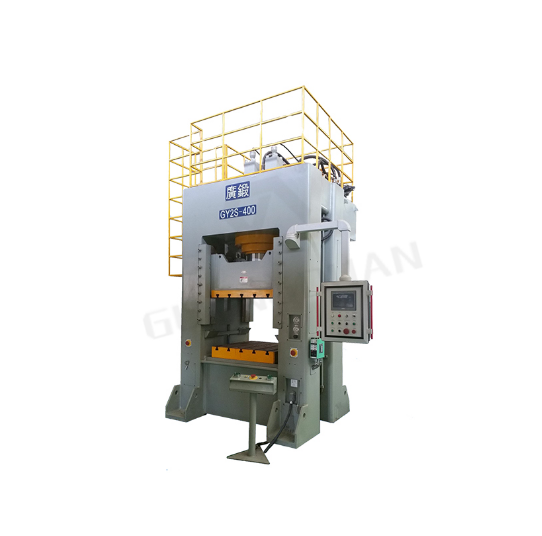
Core Design Features and Structural Advantages
High-Quality Welded Steel Construction
The GY2S Series hydraulic press is built using a high-grade steel welded box structure, which not only guarantees excellent rigidity but also ensures a robust design that significantly reduces vibrations during operation. Minimizing vibration is critical, as it maintains the highest precision levels and ensures that the machine performs reliably over extended periods. Moreover, the sleek, compact design of this machine facilitates smoother transportation and installation, enhancing its practicality for manufacturers.
Eight-Sided Full Guide Rail System
To elevate its precision even further, the GY2S Series comes equipped with an eight-sided full guide rail system. This advanced system enables the machine to retain a high degree of precision during extended production runs, a feature that is crucial in industries where consistent quality and accuracy are imperative. Over time, this structural enhancement helps maintain the machine’s accuracy while reducing wear and tear on key components.
Advanced Servo Closed-Loop Control
At the core of the GY2S Series’ impressive performance lies its servo closed-loop control system, a sophisticated configuration that includes a servo motor driver, a pressure sensor, and a Programmable Logic Controller (PLC). This system allows for real-time adjustments to be made according to the specific requirements of the mold or production process, offering users a touch-screen interface for easy and accurate control. Up to 20 different mold parameter settings can be stored, streamlining transitions between various production tasks.
Open Back Mechanical Power Stamping Machine JH21 Series: Built for Endurance and High-Volume Production
The Open Back Mechanical Power Press Machine JH21 Series has earned widespread recognition as a critical tool in the stamping industry, especially for its renowned durability and long-lasting performance. This machine is designed for mass production environments and remains a trusted option for manufacturers seeking a tool that can withstand the demanding nature of high-volume operations while ensuring precision and efficiency.
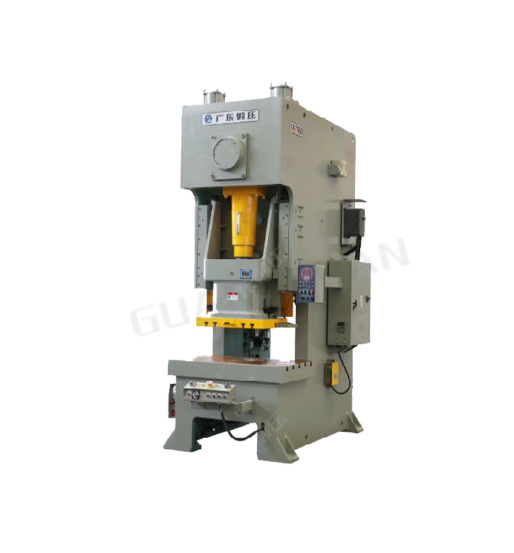
Design Innovations and Performance
Welded Steel Plate Body Construction
The JH21 Series features a body made from welded steel plates, treated with advanced techniques such as artificial aging and shot blasting passivation. This process not only prevents corrosion but also strengthens the machine’s rigidity, ensuring minimal deformation during prolonged use. Such stability is essential in maintaining accuracy, especially in environments where high-volume production is key.
Pneumatic Wet Friction Disc Clutch
A notable characteristic of the JH21 Series is its pneumatic wet friction disc clutch and brake system. This innovative design extends the machine’s service life while ensuring low noise levels and enhanced safety throughout its operation. The heat-treated gear pair and sliding pair deliver smooth, efficient transmission, contributing to the machine’s longevity.
PLC-Controlled Automation
With PLC control at its core, the JH21 Series delivers enhanced precision in every stamping operation. Furthermore, it can be integrated with an automatic feeding device, creating an automatic stamping production line that offers both high efficiency and scalability. This adaptability allows manufacturers to accommodate both small and large-scale production with ease, making it a valuable asset in industries ranging from automotive to consumer goods.
Closed Type Single Point Forge Press Machine JH31 Series: Merging Strength with Stability
When industries face more demanding forging operations, the Closed Type Single Point Forge Press Machine JH31 Series emerges as the solution of choice. Designed to withstand the toughest tasks, this press delivers outstanding strength, precision, and stability, making it ideal for industries where accuracy and durability are critical.
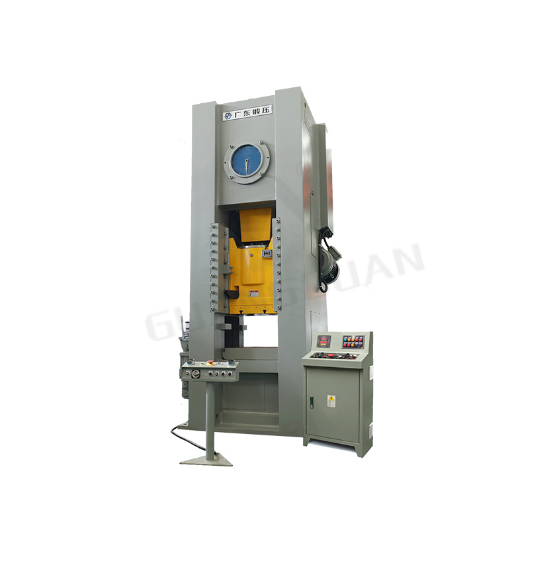
Superior Structure and Precision Retention
Monolithic Box-Type Structure
The JH31 Series is constructed with a monolithic box-type structure, which provides exceptional rigidity and strength, even under the most intense loads. This structural integrity prevents deformation during challenging forging tasks, ensuring consistent performance over time. The machine’s crankshaft, built with a high load-bearing capacity, along with its wet-type clutch, ensures long-term reliability, making it a wise investment for manufacturers.
High Guiding Precision and Easy Operation
The four-surface full-guideway slide block of the JH31 ensures high guiding precision, allowing the machine to maintain accuracy across extended production runs. Additionally, the digitally displayed, mechanically adjustable die set height simplifies die calibration, enabling operators to choose between continuous stroke, single stroke, or micro-motion based on the specific needs of their production.
High Speed Press: The Champion of Swift, Accurate Production
For manufacturers requiring both speed and precision, the High Speed Press stands out as the ultimate solution. This machine, designed to handle high stroke rates, specializes in the rapid production of metal parts, making it ideal for industries that prioritize efficiency without sacrificing accuracy.
Advanced Control for High-Volume Operations
Equipped with an advanced control system, the High Speed Press allows operators to easily monitor and adjust key parameters like speed and force. Built with a robust frame, often made of steel or cast iron, the machine ensures stability by minimizing vibrations even at high speeds, facilitating smooth, accurate production.
Conclusion: GUANGDUAN Stamping Machines – Leading the Future of Precision Manufacturing
In a rapidly evolving world where nothing short of perfection is acceptable, GUANGDUAN’s wide array of stamping machines, from the versatile Hydraulic Press GY2S Series to the swift High Speed Press, provides manufacturers with the tools necessary to stay competitive. As industries grow and evolve, GUANGDUAN’s dedication to precision, durability, and scalability ensures that its machines remain at the forefront of modern production, helping manufacturers tackle the challenges of tomorrow with confidence.
CONTACT US

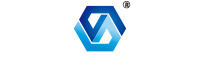
Guangdong Metal Forming Machine Works Co., Ltd.
We are always providing our customers with reliable products and considerate services.
If you would like to keep touch with us directly, please go to contact us