
In What Ways Can a 600 Ton Stamping Press Contribute to Environmental Sustainability?
In the realm of modern manufacturing, stamping presses stand as stalwarts, driving efficiency and precision in the creation of countless products. Among these machines, the 600 ton stamping press emerges as a titan, commanding attention with its robust capabilities.
Understanding the 600 Ton Stamping Press
1.1 Size, Capacity, and Applications
The GUANGDUAN 600 ton stamping press, with its formidable size and capacity, serves as a cornerstone in industrial operations. Capable of exerting immense force, this press finds its application in a diverse array of industries, from automotive manufacturing to aerospace engineering. Its versatility allows for the production of large-scale components with exceptional precision and speed.
1.2 Importance in Industrial Processes
The significance of the 600 ton stamping press cannot be overstated. Its ability to efficiently shape metal sheets into intricate forms facilitates the mass production of essential components, driving productivity and cost-effectiveness in manufacturing operations worldwide. From automotive body panels to structural components in construction, the stamping press plays a pivotal role in shaping modern infrastructure.
How It Works: Operating Principles and Components
2.1 Operational Mechanics
At the heart of the 600 ton stamping press lies a sophisticated interplay of mechanical forces and precision engineering. As raw material is fed into the press, it encounters a meticulously orchestrated sequence of actions that culminate in the formation of stamped parts. From the initial blanking stage to the final forming operation, each step is executed with precision to ensure the desired outcome.
2.2 Key Components and Their Roles
Several key components work in tandem to execute the stamping process seamlessly. The bolster plate provides a sturdy foundation for the material, while the ram exerts the necessary force to shape it. Die sets and tooling play a crucial role in defining the final product’s geometry, while sensors and actuators ensure precise control over every aspect of the operation.
2.3 Step-by-Step Process
a. Blanking: The raw material is fed into the press and positioned beneath the die.
b. Stamping: The ram descends with immense force, pressing the material into the die cavities.
c. Forming: The shaped material is ejected from the die, and ready for further processing or assembly.
Maintenance: Ensuring Smooth Operations
3.1 Regular Maintenance Tasks
Maintaining optimal performance requires a proactive approach to maintenance. Daily inspections ensure that all components are functioning as intended, while weekly and monthly tasks address wear and tear issues before they escalate. Lubrication, alignment checks, and cleaning procedures are among the routine tasks essential for smooth operations.
3.2 Common Issues and Troubleshooting Techniques
Despite meticulous maintenance efforts, occasional issues may arise. From misalignments to mechanical failures, troubleshooting techniques such as diagnostics and part replacements are employed to address these challenges promptly. Regular training and adherence to safety protocols ensure that maintenance procedures are executed effectively.
3.3 Significance of Professional Maintenance Services
While in-house maintenance efforts are crucial, professional services play a complementary role in ensuring the longevity and reliability of the 600 ton stamping press. Expert technicians possess the specialized knowledge and tools required to diagnose complex issues and implement solutions efficiently. Scheduled maintenance contracts offer peace of mind, allowing manufacturers to focus on their core operations while entrusting equipment upkeep to qualified professionals.
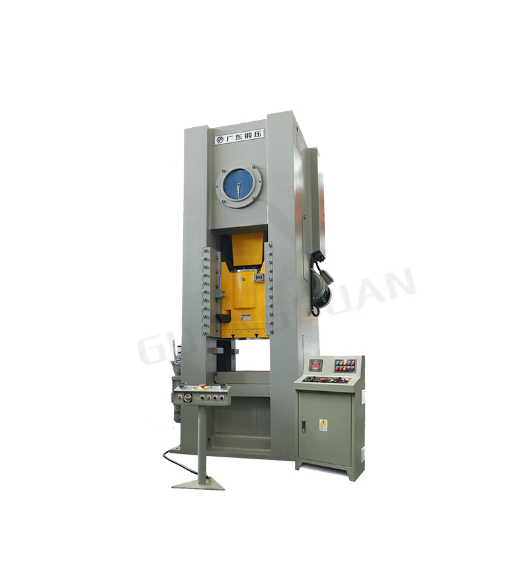
Technological Advancements: Innovations Driving Efficiency
4.1 Exploring Recent Innovations
In recent years, the landscape of stamping press technology has undergone a significant transformation, driven by a relentless pursuit of efficiency and precision. Innovations such as servo-driven presses, advanced die monitoring systems, and real-time data analytics have revolutionized the way stamping operations are conducted. These advancements not only enhance productivity but also enable manufacturers to achieve unparalleled levels of quality and consistency in their products.
4.2 The Impact of Automation
Automation has emerged as a game-changer in the realm of stamping press operations, offering unparalleled levels of efficiency and productivity. Automated material handling systems, robotic die changeovers, and adaptive control algorithms streamline production processes, minimizing downtime and maximizing throughput. As a result, manufacturers can achieve higher output volumes with reduced labor costs, driving profitability and competitiveness in the market.
4.3 Predicting Future Advancements
Looking ahead, the future of 600 ton stamping presses holds immense promise, fueled by ongoing research and development efforts. Predictive maintenance algorithms powered by machine learning algorithms will enable proactive equipment upkeep, minimizing unplanned downtime and optimizing performance. Additionally, advancements in material science and die technology will expand the capabilities of stamping presses, allowing for the production of complex geometries with unprecedented precision and efficiency.
Financial Considerations: Cost Analysis and ROI
5.1 Examining the Financial Aspects
Investing in a 600 ton stamping press entails significant financial considerations, ranging from initial purchase costs to ongoing operational expenses. The GUANGDUAN 600 ton stamping press, renowned for its reliability and performance, represents a substantial investment for manufacturers seeking to enhance their production capabilities. However, the long-term economic benefits of owning such a machine often outweigh the upfront costs, especially when considering its impact on productivity and quality.
5.2 Breakdown of Purchase Costs and Operational Expenses
The purchase cost of a 600 ton stamping press encompasses various components, including the base machine, tooling, installation, and training. Additionally, ongoing operational expenses such as energy consumption, maintenance, and material costs must be factored into the financial equation. While these expenses may seem daunting, a thorough cost analysis reveals the potential for significant savings and return on investment over the machine’s lifespan.
5.3 Conducting an ROI Analysis
Conducting a comprehensive return on investment (ROI) analysis is essential for evaluating the economic viability of investing in a 600 ton stamping press. By quantifying the expected benefits in terms of increased productivity, reduced labor costs, and improved product quality, manufacturers can make informed decisions regarding their capital expenditures. Additionally, factoring in intangible benefits such as enhanced market competitiveness and future growth opportunities provides a holistic perspective on the investment’s potential returns.
Environmental Sustainability: Balancing Industry and Ecology
6.1 Investigating the Environmental Footprint
As the manufacturing sector strives towards greater sustainability, the environmental footprint of stamping press operations has come under scrutiny. The GUANGDUAN 600 ton stamping press incorporates various eco-friendly features, including energy-efficient servo motors, regenerative braking systems, and recyclable materials. These advancements not only reduce carbon emissions but also contribute to cost savings through lower energy consumption and waste reduction.
6.2 Addressing Energy Consumption and Efficiency Measures
Efforts to improve energy efficiency are central to the sustainability initiatives of modern manufacturing facilities. The GUANGDUAN 600 ton stamping press employs state-of-the-art energy management systems, allowing for precise control over power consumption during operation. Additionally, optimization techniques such as idle mode activation and load balancing further enhance energy efficiency, minimizing environmental impact without compromising productivity.
6.3 Discussing Waste Management Practices
Effective waste management is another crucial aspect of environmental sustainability in stamping press operations. The GUANGDUAN 600 ton stamping press integrates advanced waste collection systems and recycling technologies, allowing for the efficient disposal and reuse of scrap materials. By minimizing waste generation and maximizing resource utilization, manufacturers can reduce their environmental footprint while conserving valuable resources for future generations.
6.4 Highlighting Industry Initiatives
Across the industry, manufacturers are embracing sustainable practices and initiatives to minimize their environmental impact. Collaborative efforts such as industry-wide recycling programs, energy efficiency standards, and eco-friendly material sourcing initiatives are driving positive change and promoting a more sustainable future for manufacturing. By aligning with these initiatives and investing in environmentally responsible technologies, manufacturers can play a pivotal role in mitigating climate change and preserving the planet for future generations.
Conclusion
The GUANGDUAN 600 ton stamping press stands as a testament to engineering excellence and manufacturing prowess. Its formidable capabilities and precise execution make it an indispensable asset in a wide range of industries. By understanding its operational mechanics, prioritizing regular maintenance, and leveraging professional services when needed, manufacturers can harness the full potential of this powerhouse machine, driving innovation and efficiency in the modern manufacturing landscape.
CONTACT US

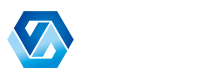
Guangdong Metal Forming Machine Works Co., Ltd.
We are always providing our customers with reliable products and considerate services.
If you would like to keep touch with us directly, please go to contact us